Contents 目次
プロフィール
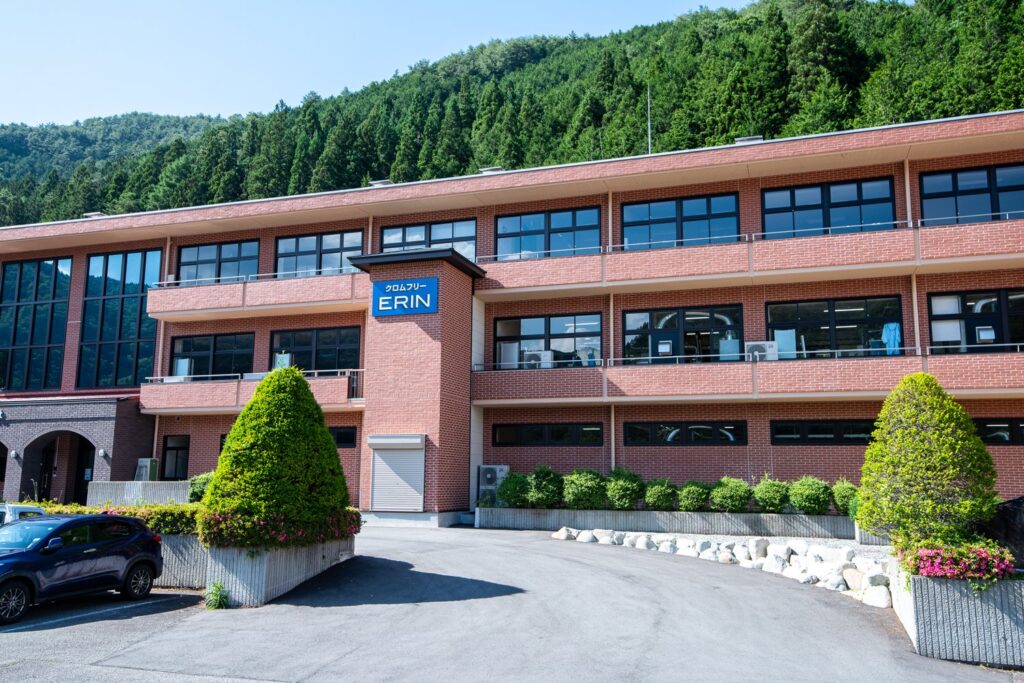
豊実精工株式会社
1985年岐阜県にて創業。機械加工事業、レイデント事業を軸にペレットストーブ販売事業などを展開している。レイデント処理とは電気メッキ的製法で処理した被膜と機能性を有するコーティングによる複合処理のこと。また、CNC工作機械を100台以上保有しており、加工から企画設計組み立てまでの一貫生産が可能なほか、小部品から大型部品までトータルに対応できる点が強みだ。2022年にはクロムメッキに替わる革新的技術「ERIN」を開発。自然環境に恵まれた岐阜県下呂市馬瀬で廃校となった旧馬瀬中学校校舎を改修し、ERINのモデル工場を設立。ここを拠点に、10年後、15年後にはERINを核とした企業城下町の構築を目指している。
クロムフリー表面処理技術ERINとは
ERINは六価クロム化合物のような環境や人体に有害な化学物質を使用するクロムメッキではなく、環境や人にやさしく資源としても豊富に存在する酸化アルミニウムを用いた完全クロムフリーの表面処理技術だ。通常のメッキはメッキ液に浸して通電させ、金属を析出させるウェットな手法で皮膜を生成するが、ERINはこのメッキ液を使用せず、低真空下のドライな環境で原料を高速で飛ばし、製品に衝突させて成膜する。有害物質を使用しないため、従来のメッキ工程で懸念されていた作業者への健康被害リスクがなく、万が一地震等の災害が起きても六価クロム化合物が工場外に漏れ出す心配はない。
「ERINは安全性だけでなく、表面処理の性能についても従来のクロムメッキを上回っています。メッキ作業が常温処理で行えるため、熱による歪みや寸法変化も生じませんし、膜厚1~3μmの皮膜で耐摩耗性はクロムメッキを超え、さらに1~6μmで優れた防錆能力を発揮し、マイナス70~750℃の耐熱性、Hv1,200~1,400の皮膜硬度も備えています」
表面処理に求められる耐摩耗性や耐食性、摺動性、耐熱性などを備えながらも、環境や人体にも悪影響を及ぼさないERIN。世界のメッキ業界やものづくりなど、巨大な市場を変えうる革新的技術といえる。
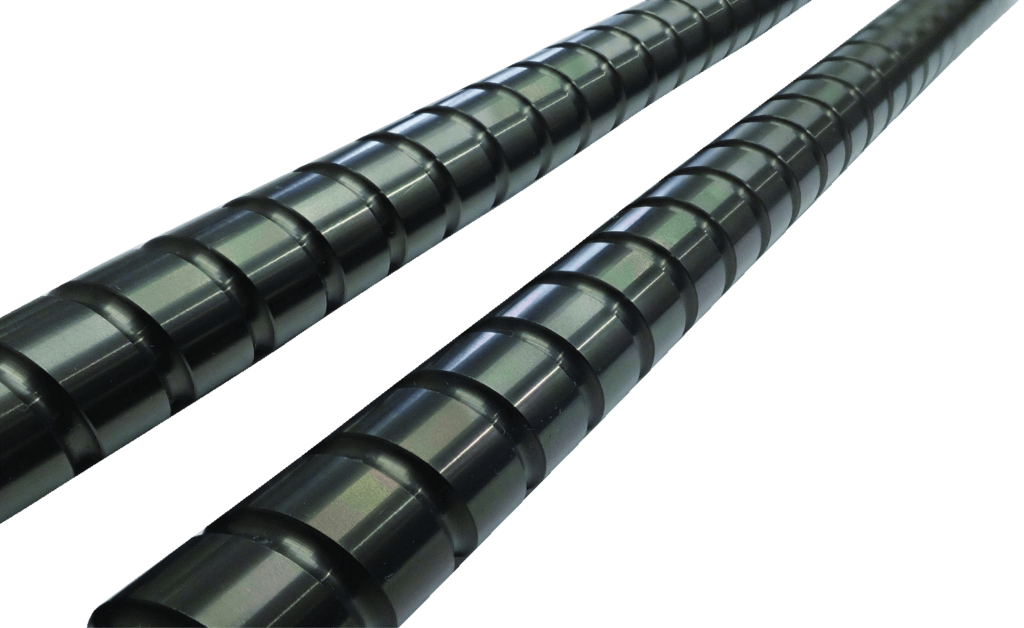
表面処理業界の常識が変わるERINはどのようにして生み出されたのか
ERINの開発がスタートしたのは9年前のことだ。当時の豊実精工はレイデント事業を柱としていたが、環境問題への関心の高まりもあり、六価クロムを用いるレイデントメッキはEUを中心に規制の動きが活発化していた。例えば、ドイツでは2024年から六価クロムの規制を本格化させることがすでに決まっている。日本ではまだ規制の動きはないが、いずれ世界の潮流の影響を受けることは確実だ。
「いつレイデントがなくなるかわかりません。そのときに備えて、日本もリスクをとってでも挑戦すべき。そんな想いから当社は代替技術の開発をスタートさせたのです」
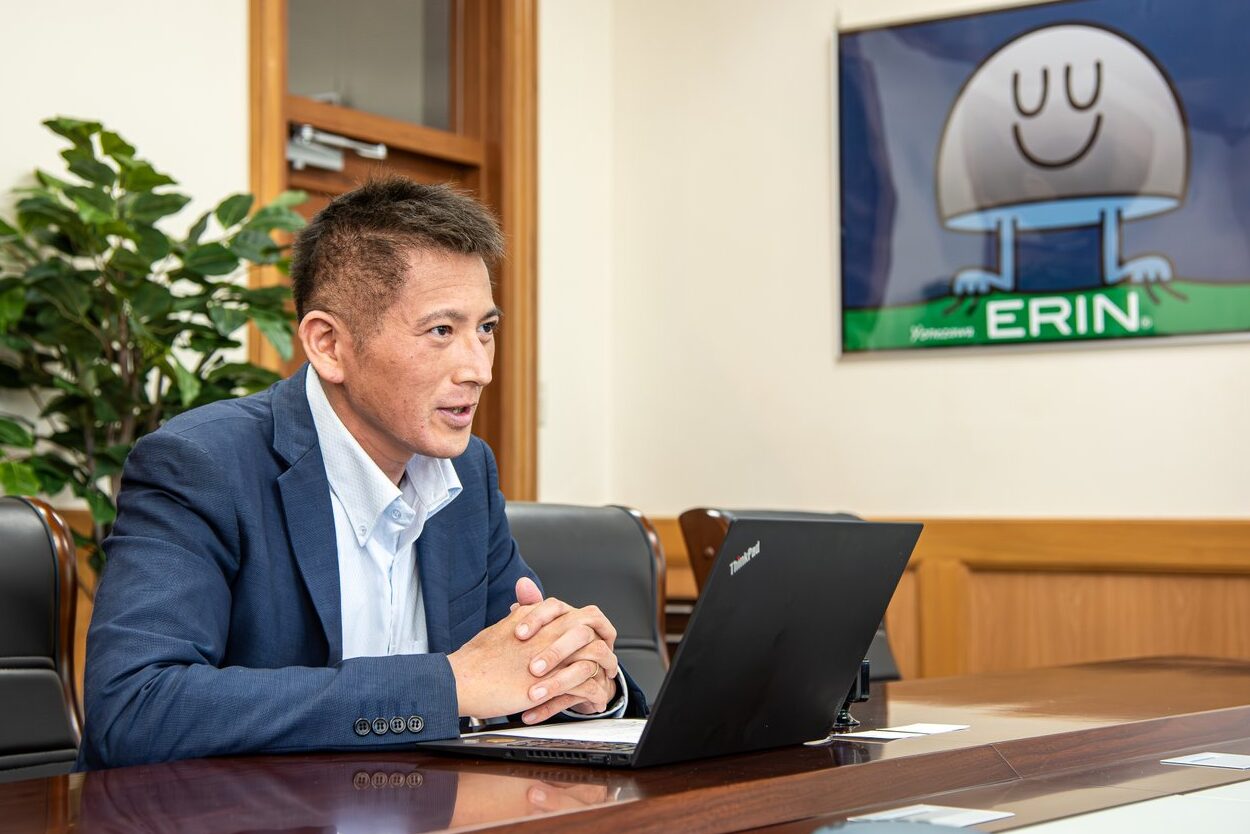
開発のテーマは、薄くて防錆能力が高く、なおかつクロムフリーであること。だが、開発への道のりは一筋縄ではいかなかった。それまでのレイデントメッキは低温で溶かした原材料に製品を浸漬する「どぶづけ」と呼ばれる方法で行われていたため、まずは同様の方法で代替技術の開発を試みたのだが、うまくいかなかった。「暗闇の中、手探りで光をつかみにいくような状態だった」と今泉氏は当時を振り返る。
代替技術の研究を始めてから4年後、光明が見えた。転機になったのは、とある展示会で産業技術総合研究所のブースに社員が立ち寄った際、AD(エアロゾル・デポジション)法という技術に出会ったことだ。
「AD法とは、製品に材料を高速で飛ばして衝突させることにより成膜させる『常温衝撃固化現象』を活用した技術です」
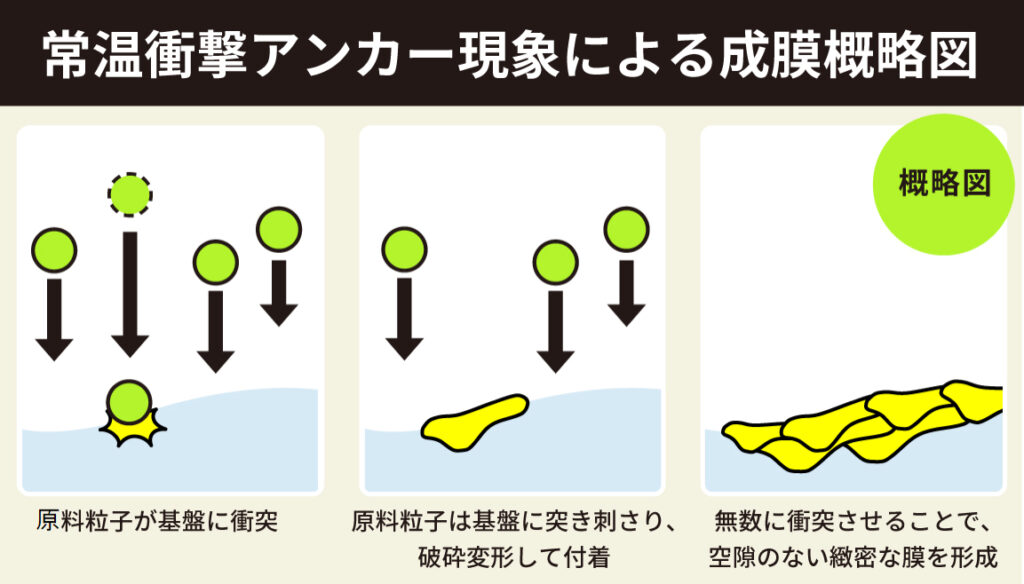
材料をどぶづけするのではなく、材料を飛ばして成膜するAD法はまさに逆転の発想だった。さっそくAD法を用いた表面処理に取り組んだ豊実精工だったが、当初は課題も多かった。例えば、メッキで重要な耐食性がなかなか確保できなかったことだ。耐食性を検査する塩水噴霧試験では、製品の表面のほとんどが錆びてしまっていたという。
そんな苦境を脱する原動力となったのが、社長の強力なリーダーシップだった。
「塩水噴霧試験で、なぜか1ヵ所だけ錆びないところがあったのです。それを見た社長が、『その部分が錆びていない条件を見つければどうにかなる』と方針を定めたことで、社員も前を向いて進むことができました」
方針を決めてからの同社の動きは早かった。岐阜本社と米沢事業所の2拠点で同時に開発を進め、薄膜でありながら良好な防錆能力が実現された。約3年をかけて十分な耐摩耗性や耐食性などの課題を着実にクリアし、ついに求める性能を実現するERINの装置が完成した。
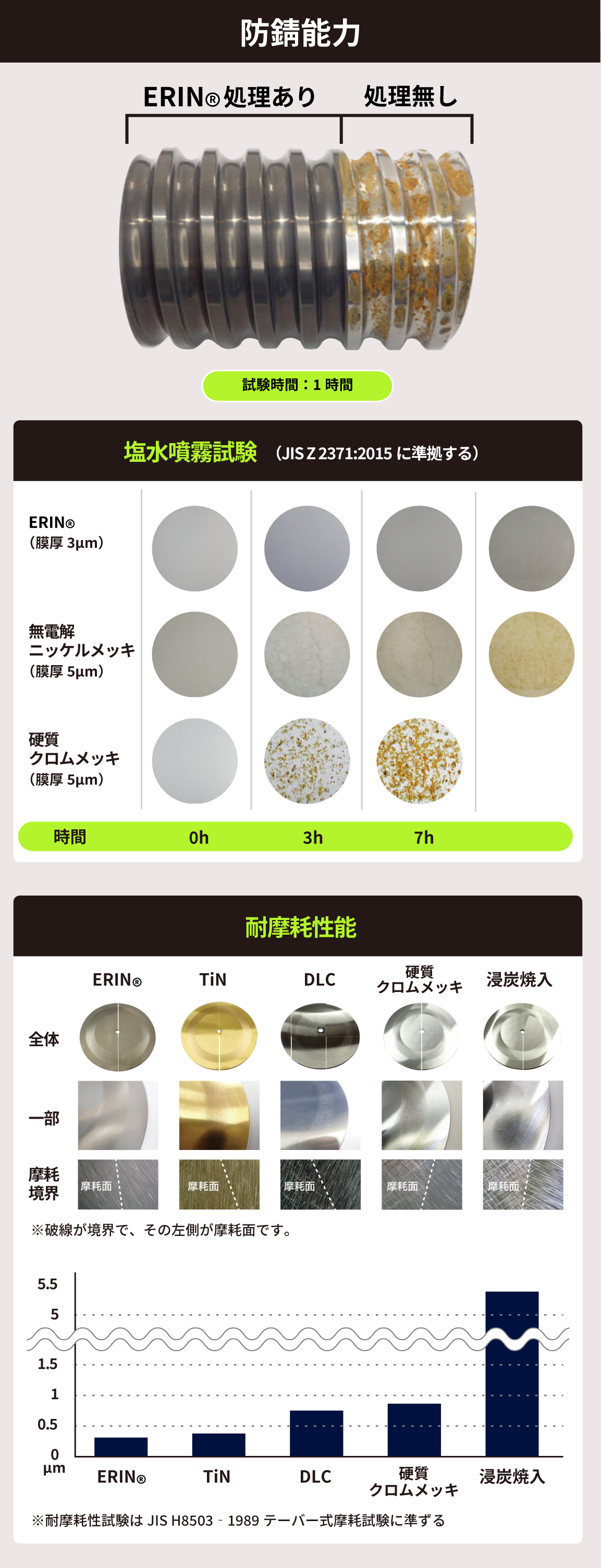
だが、課題はまだあった。AD法はもともと平面を対象とした技術であり、立体や球体など複雑な形状の製品は対象外だったのだ。これでは従来のクロムメッキ処理の完全な代替にはならない。
そこで豊実精工は独自に開発を行い、立体物にも対応できるよう平面以外のものにもメッキ処理を施すことに成功した。それを可能にしたのが、同社が創業から培ってきた機械加工技術だ。こうした装置を開発する場合、まずは試作機をつくってから量産化に入るのが一般的だが、同社は本社工場、駒ヶ根工場、中国工場で合わせて約100台のNC加工機を保有しており、自前で装置の部品加工が行える。この強みを活かし、同社は馬瀬、米沢、福井大野の3拠点にすでに4台ずつ、計12台の量産試作機をそろえるなど、驚くべき速度で開発を進めていったのだ。
「仮に当社が専業のメッキ屋であったなら、装置を製造することはできず行き詰まっていたと思います。当社は39年前に汎用フライス数台からスタートし、機械設計、機械加工、組立、レイデントと事業を拡大してきました。そうした創業からの積み重ねがERINで結実したのです」
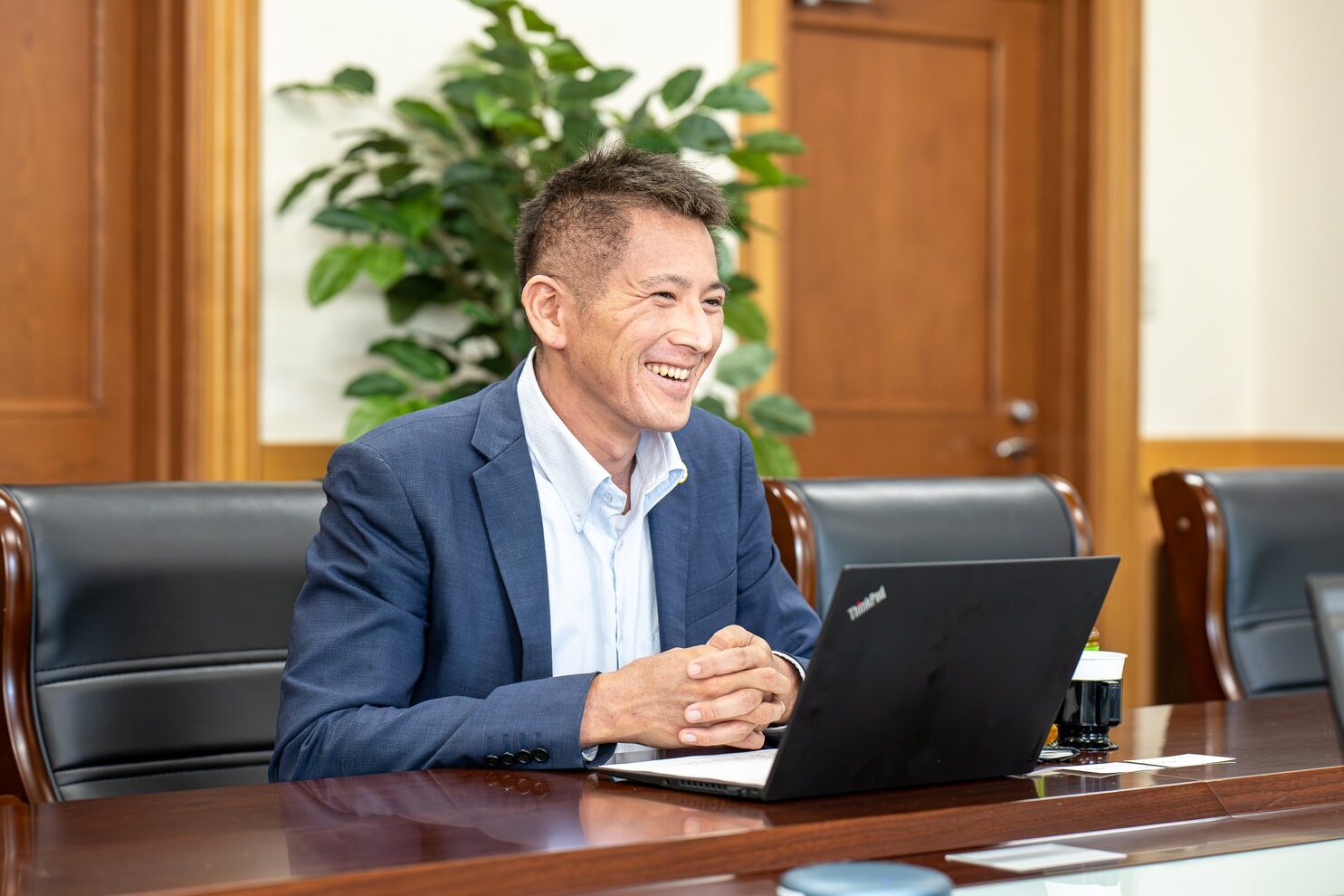
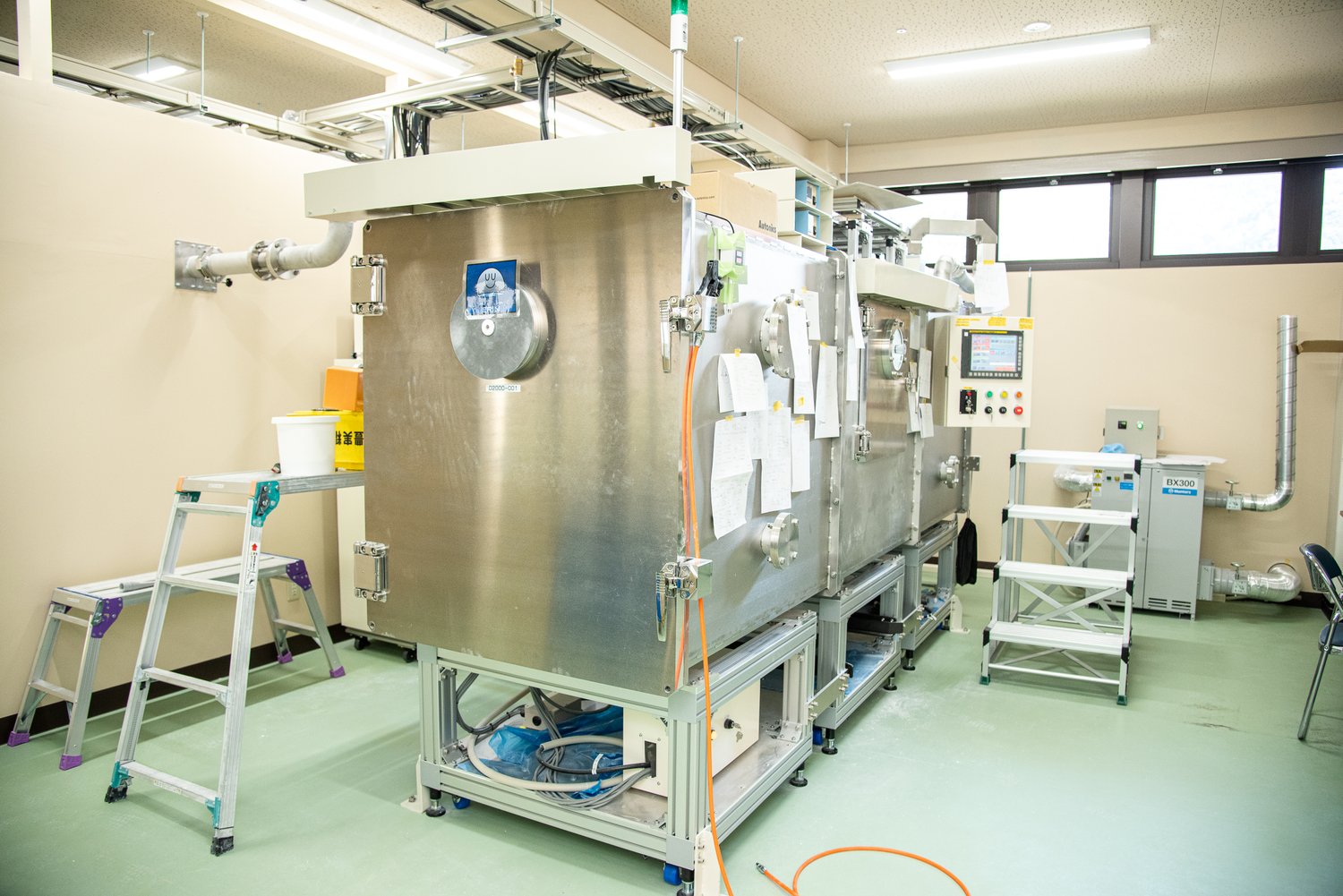
ERINの現状と今後の展望
革新的なクロムフリー技術であるERINは今後、世界をどう変えていくのか。
「クロムの中には非常に低コストなものもあり、そうしたクロムまで含めてすべてのクロムメッキを置き換えられるわけではない」と今泉氏は言う。当面の間、ERINが置き換えていくと見られるのは硬質クロムとDLCだ。それでも日本だけで1,000億~2,000億円の市場規模があるという。
「硬質クロムメッキはローラーによく使用されています。例えば、半導体用フィルム製造装置や食品包装機、医療装置などのローラーなどです。現状、ERINで処理できるのは奥行き300mm、横800mm、Z軸が250mmまでなのですが、現在長尺専用試作機を開発中です。4メートル以下の製品を成膜出来るように開発中です。あまりにも大きなローラーは無理ですが、ある程度のサイズまでなら置き換えが進むのではないでしょうか」
すでに半導体装置向けの小物部品についてはリピートオーダーも来ており、ヨーロッパや中国からも反響があるという。まずは六価クロムの規制が進むドイツで、現地のクロムメッキ業者との連携を足がかりにヨーロッパへの展開を目指す計画だ。
世界に進出するのであれば、さまざまなニーズに対応するためにもさらなる装置の改良を進めていく必要がある。
例えばサイズ展開だ。シャフトであれば直径450~500mm、長さ4,000mmを処理できる装置の制作を予定している。高真空チャンバーではできないようなサイズの表面処理が可能な機械の開発も視野に入れている。
豊実精工は酸化アルミニウム以外の材料についても自社で開発を進めている。というのも、酸化アルミニウムが医薬や食品業界で使用される強アルカリに溶けてしまう課題があるからだ。また、厚膜や絶縁性を求められる製品への需要もあるという。
処理スピードも重要だ。現在のERINは1本のノズルを固定し、製品を動かして成膜する仕組みだが、これだと製品を動かすためのスペースが必要になり、処理も1方向ずつしかできない。そこで同社は、ノズルを動かして工作機のような多軸表面処理を可能にする仕組みを開発中。これにより対応できる製品のサイズも大きくなり、多軸に処理することで時間も短縮できる。処理速度を上げ、さらにできるだけERIN成膜を止めずに稼働させることでコストダウンにもつなげられるのだ。
現在、ERINは岐阜県下呂市馬瀬の廃校を改修した工場で稼働している。通常、六価クロムによるレイデントメッキを行う工場は環境への影響を考慮して建てられる場所が限定されるが、環境に悪影響を及ぼさないERINにはそうした制限がない。鮎も釣れるほどのきれいな馬瀬川が近くを流れる馬瀬の工場は、まさにERINの特長を体現した場所といえる。この馬瀬工場のメンバーは13名。ほかの2拠点と合わせるとメンバーは30名に達しており、豊実精工がERINにかける本気度が伝わってくる。
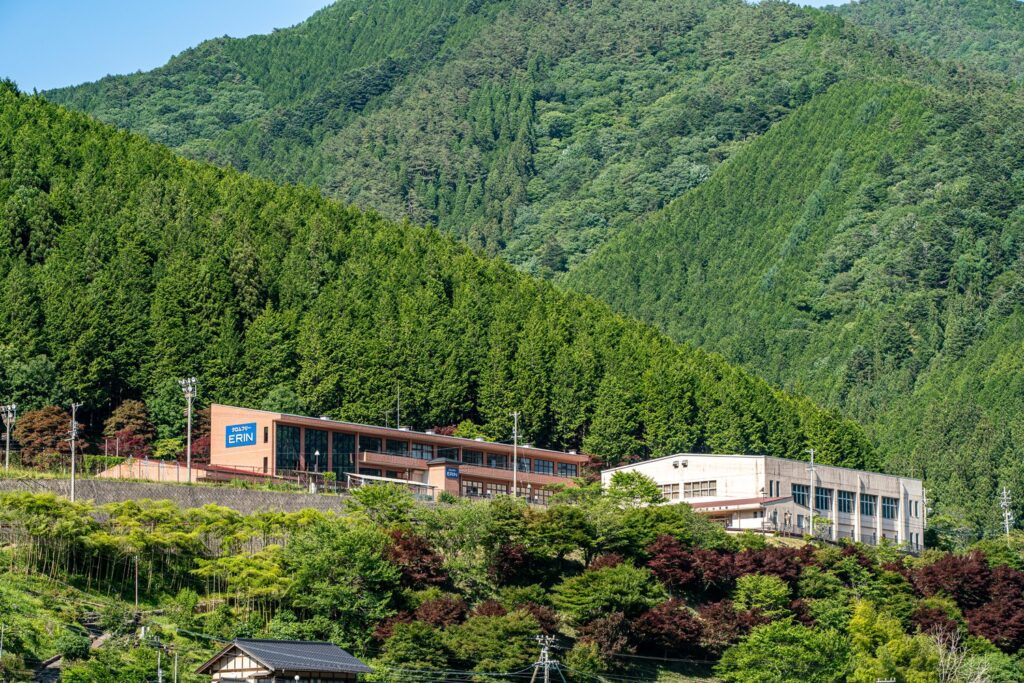
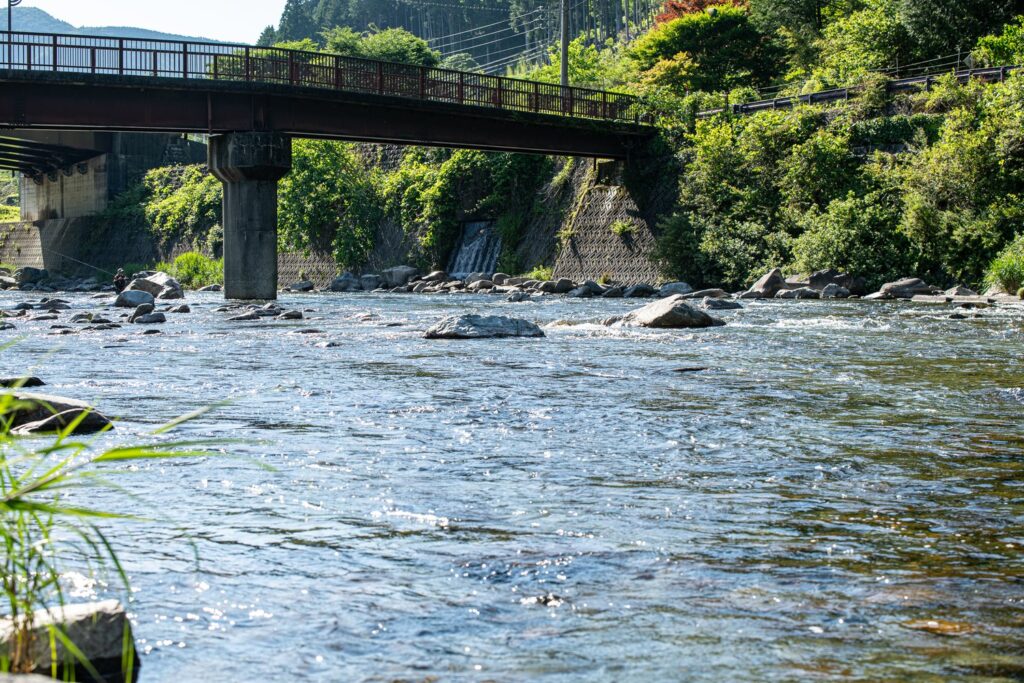
ERINが世界を変えるきっかけに
ERINという名称は、アメリカの環境活動家であるエリン・ブロコビッチに由来している。エリン・ブロコビッチは巨大企業が引き起こした六価クロムによる環境汚染と健康被害に立ち向かい、訴訟を起こして多額の賠償金を勝ち取ったことで知られる人物だ。エリン・ブロコビッチのエピソードは映画化もされているため、知っている人もいるだろう。
現在、自動車用蓄電池の材料調達からリサイクルまで、ライフサイクルに関わる情報を記録する「バッテリーパスポート」が欧州で発表され話題となっているが、同様の流れが今後クロムメッキにも起きる可能性は十分に考えられる。六価クロムの有害性を世に知らしめたエリン・ブロコビッチのように、ERINがクロムフリーな世界へのきっかけをつくるのかもしれない。