Contents 目次
プロフィール
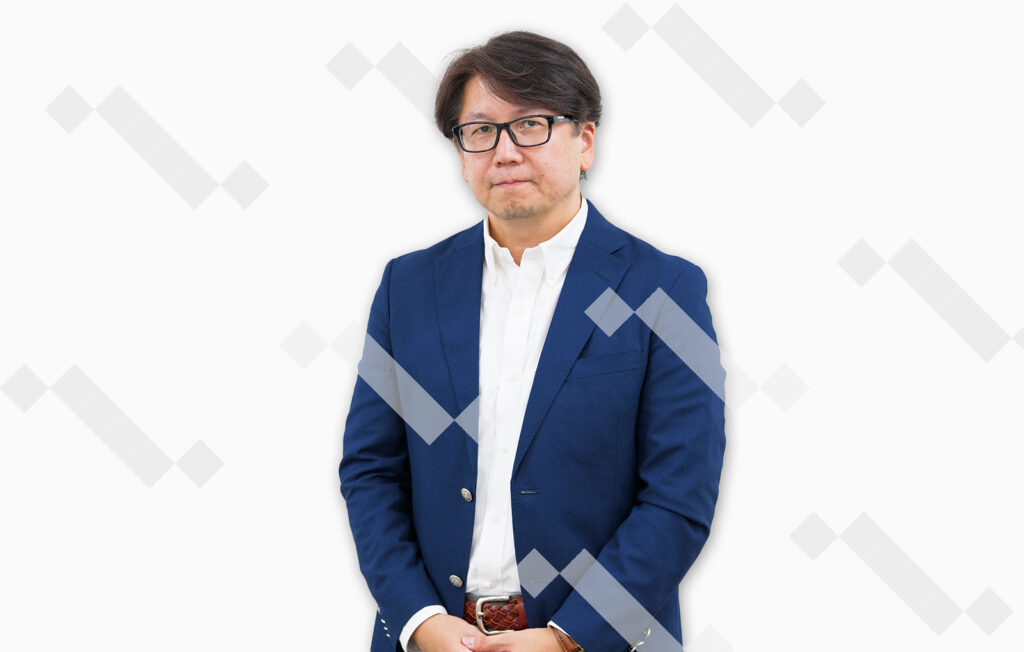
マイクロ波化学株式会社 取締役CSO(最高科学責任者)塚原保徳さん
2003年大阪大学大学院理学研究科博士後期課程修了。2004年大阪大学大学院工学研究科・特任研究員、2006年大阪大学大学院工学研究科特任准教授。2007年、吉野巌さんとともにマイクロ波化学株式会社を創立。取締役CSO(最高科学責任者)として研究開発を主導する。
ラボスケールで停滞していたマイクロ波の産業応用
波長約1mm~1m(周波数300MHz~300GHz)の電磁波であるマイクロ波。マイクロ波は誘電体に直接エネルギーを伝えられるという大きな特徴があり、省エネや新素材開発、装置や設備のコンパクト化など、従来の加熱プロセスにはない効果が期待されるとして注目を集めている。
「マイクロ波は、学問より民生の産業化が先行した珍しい事例なのです。マイクロ波の技術は、電子レンジに使われ、安全で便利、かつ効率的な加熱方法だということで、一気に各家庭に普及しました。業務用の国産電子レンジが発売されたのが1961年。マイクロ波がラボスケールで多くの実証が行われるようになったのは1980年代に入ってからです。数万報に及ぶ国際論文も公表されていて、総じてポジティブな結果が出ていましたから、各国の大手化学企業がこぞってスケール化、産業化にチャレンジしました」
マイクロ波の応用対象の中でも、化学産業で消費されるエネルギーをマイクロ波へ置き換えることにはとりわけ大きな期待がかけられた。化学産業の製造プロセスにおいて、リアクター(反応炉)で化学反応を起こす際に使われるエネルギー量は莫大だ。経済産業省によると、化学産業は製造業におけるエネルギー消費量の実に約40%を占めている。また、産業部門における二酸化炭素の排出量も鉄鋼に次いで多く、約15%に上る。
しかし、各国の大手化学企業が総力を挙げて、スケール化・産業化に挑んだにもかかわらず、2010年頃になってもマイクロ波の実証はラボスケールで停滞していた。スケールアップをあきらめてクローズする化学企業も多くあった。
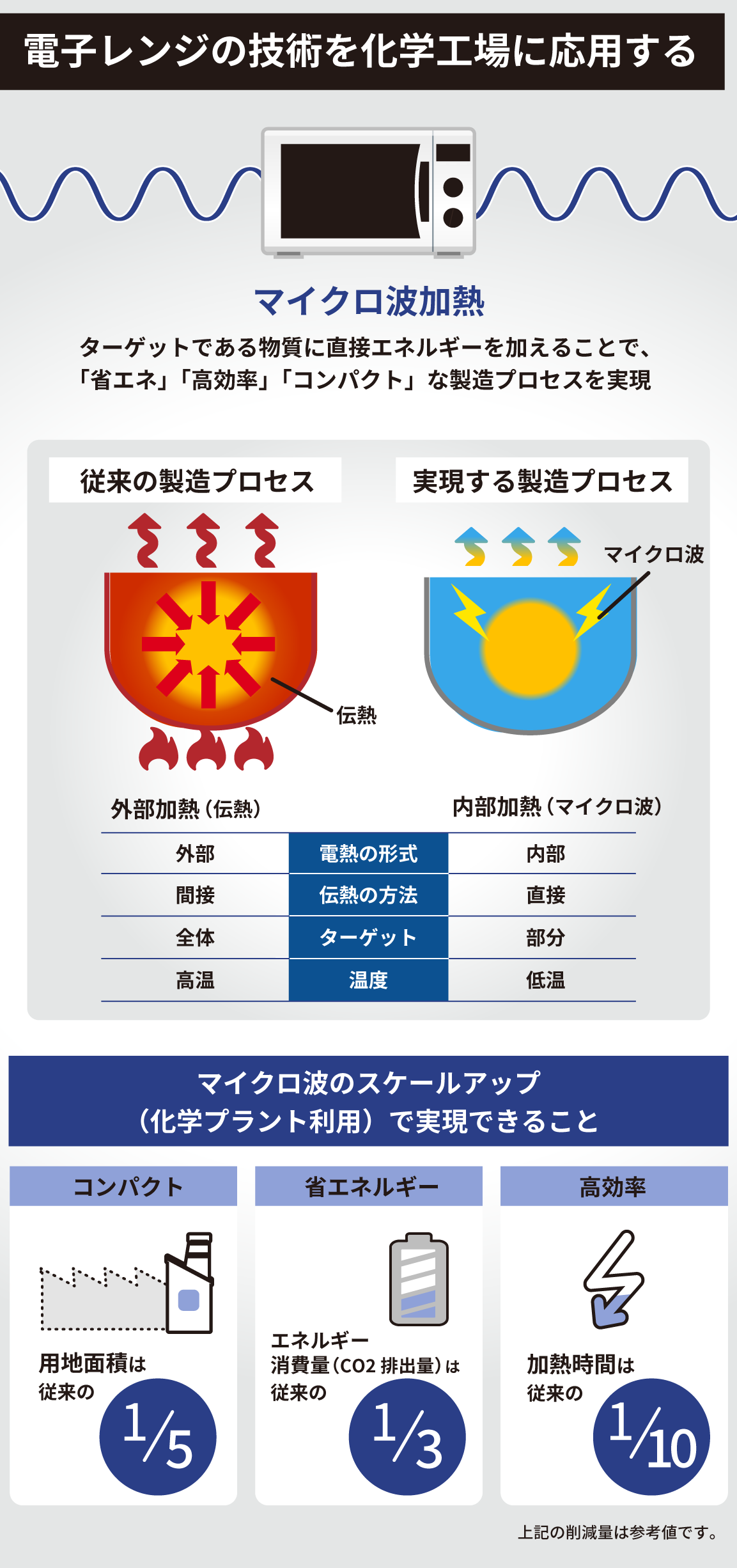
マイクロ波で、化学産業を変え、世界を変える
塚原さんがマイクロ波と出合ったのは、大阪大学大学院理学研究科を修了後、ポスドクとして、ナノ粒子、光化学、マイクロ波がテーマの研究室で勤務していたときのことだ。そこへ、日本で新技術を探していた吉野巌さん(現・マイクロ波化学株式会社代表取締役社長CEO)から研究室にコンタクトがあり、2人は初めて接点を持つ。吉野さんは三井物産株式会社を辞めてアメリカでMBAを取得し、日本に一時帰国していた。
「そのときのターゲットであったナノ材料は彼のアイディアとうまくマッチしなかったのですが、吉野と私は気が合いました。私はシーズで日本の産業を強くしていくことに強く関心があったので、テクノロジーで世界を変えたいという一念が共通していたのでしょう。1年ほどコミュニケーションをとっていたところ、彼からバイオディーゼルの事業化について話がありました。2006年頃のことだったと思います」
2005年といえば、アメリカの包括エネルギー法において、再生可能燃料基準が策定され、バイオディーゼル燃料の需要が高まっていたころだ。バイオディーゼルの原料は植物性や動物性の油脂だが、日本には原料がない。そこで2人は、マイクロ波を使って工場の廃油からバイオディーゼルを作り出す技術を編み出し、2007年にマイクロ波環境化学株式会社(後のマイクロ波化学株式会社、以下MWCC)を立ち上げた。
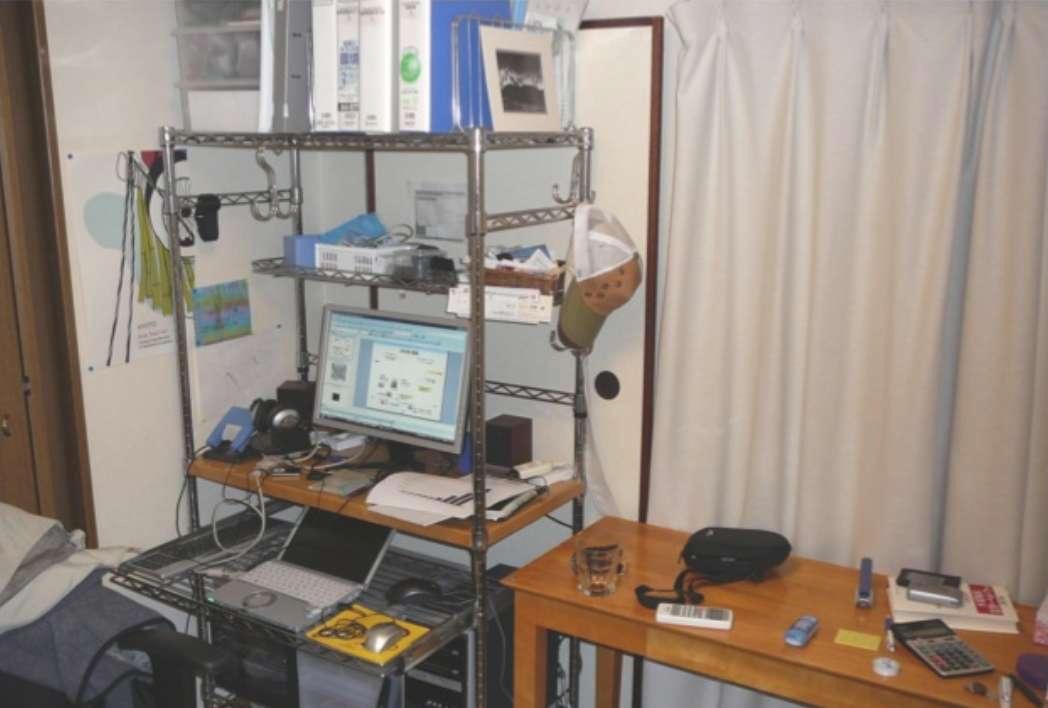
塚原さんと吉野さん2人で創業したマイクロ波化学。自宅であるマンションの一室からスタートした:マイクロ波化学提供
「私たちにとって、バイオディーゼルは手段のひとつでした。マイクロ波技術によって化学産業を変えて、重厚長大であった製造プロセスを省エネ、高効率、コンパクトなプロセスに変えたり、今までになかった物質を創造したり、これまで高くて使えなかった材料が安く使えるようにしたい、そう思って会社を立ち上げたのです」
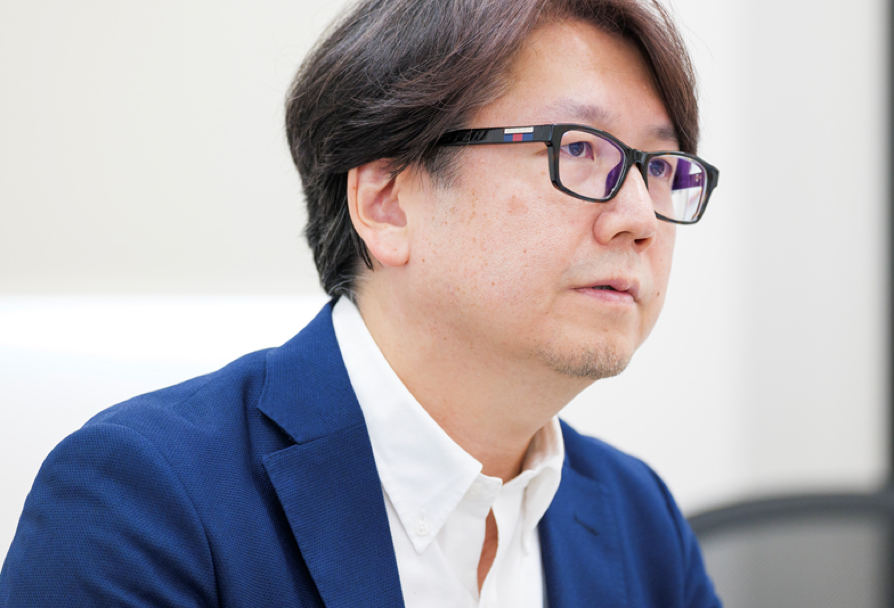
強い思いを持って会社を立ち上げたものの、日本ではバイオディーゼルが浸透せず、設立からほどなくして会社がつぶれかねない状況に陥った。その当時、塚原さんたちは、コアなマイクロ波技術を知見として売り、収益を上げようとしていた。
「当時の化学産業は、1970年代にできたプラントの入れ替わり時期だったので、新しい技術を求めていました。
マイクロ波を使った製造プロセスは、省エネで高効率、未利用の資源エネルギーを使える技術として、経営層に響きました。しかし、安全を旨とする化学プラントの現場では、実証されていない新しい技術、プロセスを受け入れることへの壁が大きかったのです。
そこで、私たちは2011年に神戸に少量危険物対応のパイロットプラント(以下、神戸プラント)を建設し、東洋インキ株式会社に新聞インキの原料として使われていた脂肪酸エステルの出荷を開始しました。しかし、それでもおもしろいと関心を持ってもらうところで話が止まってしまう。神戸プラントでは化学品を作るために必要な消防法『危険物製造所』の認可が下りずに量産ができなかったんです。
化学産業に受け入れてもらうには、もうやるしかない。量産が可能なことを証明するために自社プラント設立に舵を切りました。会社の方向性を大きく変える重い決断でしたが、結果的には今につながる勇断だったと思います」
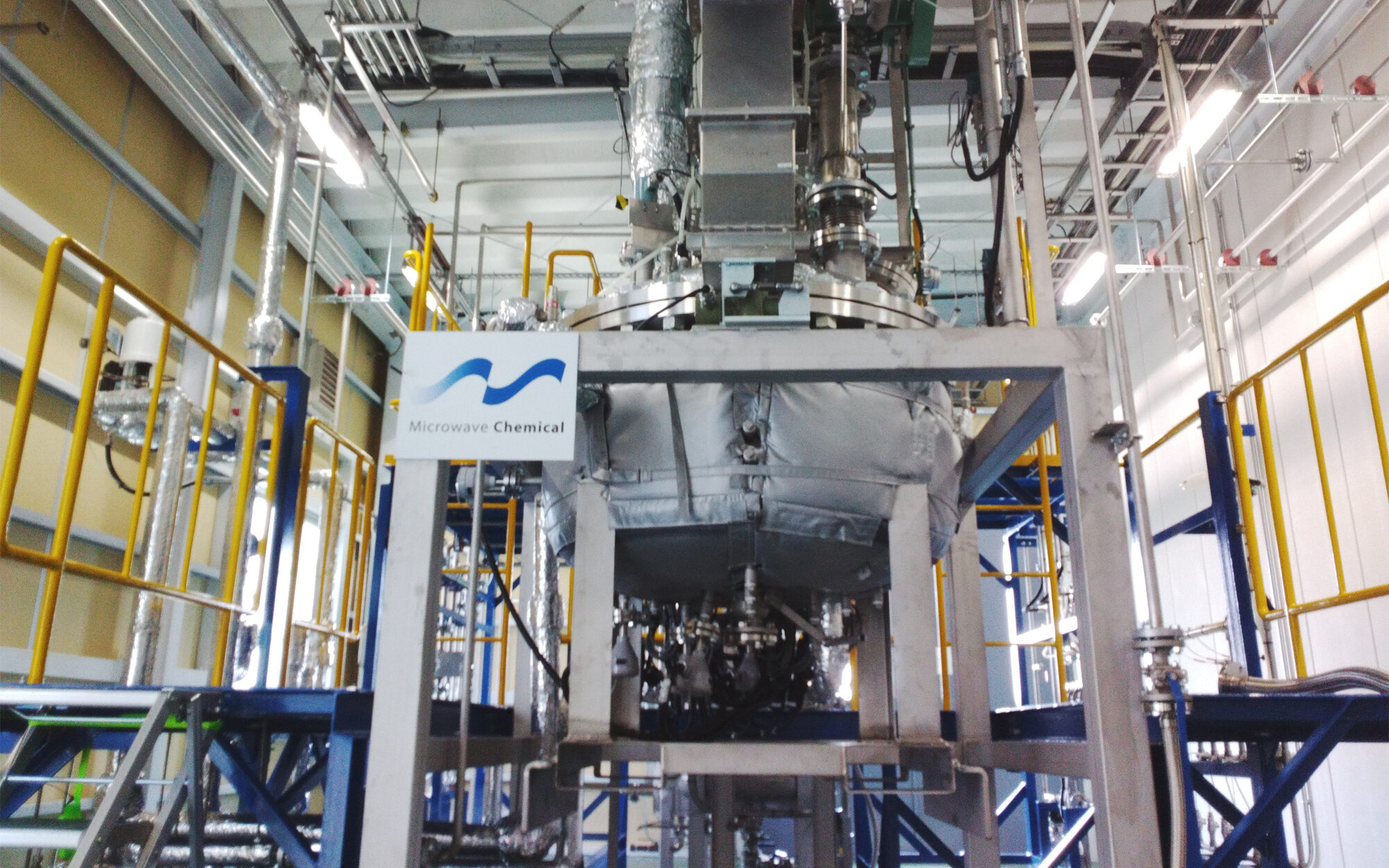
スケールアップの肝は、物質ごとの反応条件と使い方をデザインすること
長年、マイクロ波の産業利用が困難といわれていた、リアクターのスケールアップとマイクロ波の制御。化学業界では、不可能なものとして取り組み自体が終わっていたにもかかわらず、MWCCは不可能を可能にした。その要因は何だったのだろうか。
塚原さんは「マイクロ波のデザインが不十分である」と考えた。
「マイクロ波の最大の特徴は、ある特定の物質だけに選択的にエネルギーを伝達できること。例えば、原理的には3層のフィルムのうち、真ん中だけにエネルギーを加えることもできます。
それがなぜできるかというと、物質ごとにマイクロ波を吸収する能力や周波数が異なるからです。以前は、物質のマイクロ波吸収能の測定・分析・解析が不十分だったため、自由に使いこなすことができませんでした。
そこで私たちは、測定装置を自前で作り、物質ごとのマイクロ波に適した反応条件をデータとして蓄積していきました。液体、固体、粉体、フィルムなど、さまざまな状態の物質が、どのような条件下でどのくらいマイクロ波を吸収するのかを把握できれば、効率的なマイクロ波の照射プロセスをデザインすることができるのです」
MWCCでは、マイクロ波に適した反応条件を『反応系デザイン』と呼んでいる。物質の吸収特性、温度と周波数によって変化する複素誘電率の測定データをライブラリー化。このデータをもとに、被加熱物が最も効率良くマイクロ波エネルギーを吸収するような、温度条件やマイクロ波周波数を選定することができる。ライブラリーの数は液体・固体など合わせて5,000以上、一般的に使用されやすいものからデータベース化され、一部は顧客に開示している。
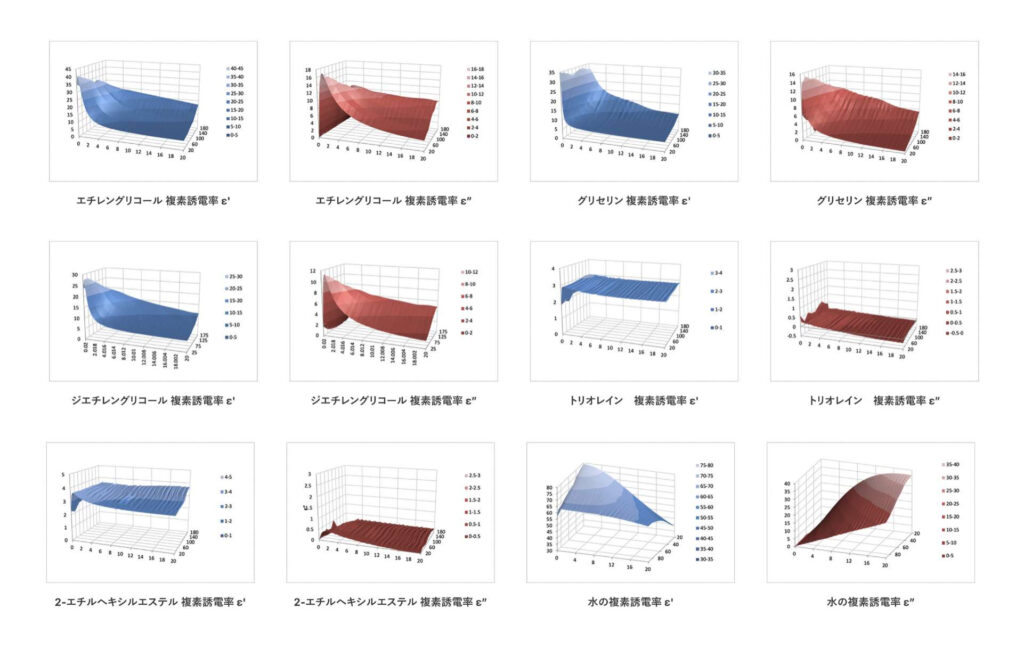
「反応系デザインを用いてラボ実験を行い、マイクロ波の反応系が最適化されたら、今度は、どのように電界を分布させるかというデザインが必要です。我々はこれを『反応器デザイン』と呼んでいます。
電子レンジで食べ物を加熱したときに、たまに加熱ムラがあると思いますが、こうしたことが実際の工場で起きるようなことがあれば、実用化は難しい。反応系デザインをベースに、従来の反応器にはとらわれず、最適なマイクロ波が分布するような反応器の形状、プロセスをデザインする必要があるのです」
MWCCでは、本社にある2台のスーパーコンピューターを用いたシミュレーション技術で、目に見えないマイクロ波の最適化を図る。シミュレーション上でPDCAを回し、可能な限り精度を高めてから試作機の製作に移行する。そのため、試作機の製作回数、改造を大幅に削減することが可能なのだ。
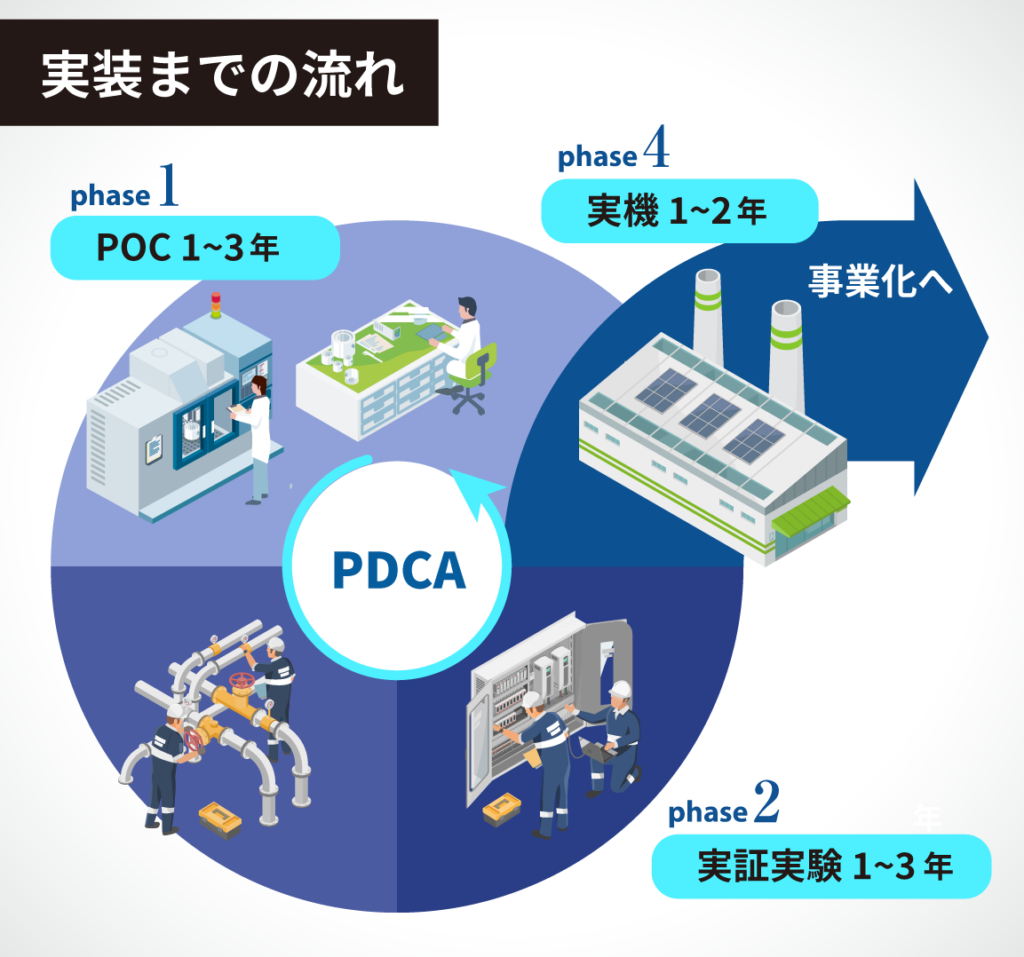
「マイクロ波を効果的に吸収させるための反応系デザインと、反応系デザインを具現化するための反応器デザインを軸とした技術プラットフォームにより、競争力のあるマイクロ波プロセスを構築できると考えています。開発した技術を実際の工場で使ってもらうにはこの2つが何より重要であると考え、デザインに必要な要素技術群を設定しました。
設立当初から2025年くらいまでの要素技術を、基礎物性評価、シミュレーション、制御、基盤機構の4カテゴリーにて、ロードマップを引いていたのです。そのロードマップにもとづいて、基礎物性評価においては自前の測定・解析装置を作り、得られたデータを3次元ライブラリーとして蓄積してきたのです。これは当社の大きな財産です」
MWCCはこうして、研究と実績を積み重ね、独自のフローを確立し、マイクロ波のスケールアップを実現させた。2014年に世界初の大規模マイクロ波化学工場が誕生すると、「マイクロ波を使って、本当にものづくりをしている」と驚きをもって化学産業にその存在が広まり始めた。そして、多様な業界の企業との共同研究がスタートしたのだ。クライアントへの本格導入前にパイロットプラントを検証する実証棟も造り、多様な製造プロセスに対応できる体制を整えた。現在、実証棟にある14室すべてが埋まっており、新たな棟の建設計画が進んでいる。
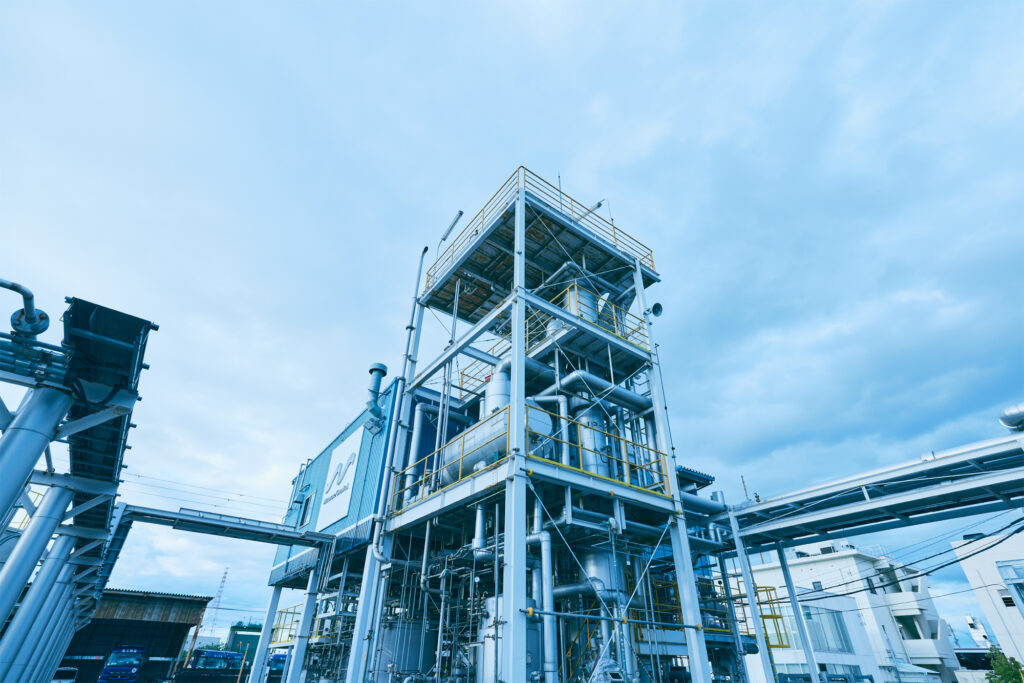
不可能と考えられていたスケールアップの成功要因は、「やりきる力」と「やり続ける力」
こうしてマイクロ波のスケールアップを成し遂げたMWCCだが、当初は周囲から「無理だ」「やめておいたほうがいい」という声が多かった。なぜ、これらの反対を振り切って茨の道を選び、化学産業を変革する未来を引き寄せることができたのだろうか。その理由は、技術力だけではない、と塚原さんは話す。
「マイクロ波のスケールアップ実現化は、勝算があったとはいえないし、損得勘定だけなら絶対にやらなかったでしょうね。
ですが、従来にはないエネルギーの伝達手段であるマイクロ波に、大きな可能性を感じていました。
マイクロ波がスケールアップしたら、従来の製造プロセスを根本から覆し、社会にプラスのインパクトを与えることができる。100年変わらずにいた化学産業界にイノベーションを起こすことができる。世界を変えるかもしれない技術に挑んでいる。それが、大きなモチベーションでした。挑戦すること自体が楽しかったのです。
成功した一番の理由はと聞かれたら、一言でいうと気合いでしょうか(笑)。具体的には、『やりきる力』と『やり続ける力』です。この2つは、いっしょに働くチームでも重きを置いている力であり、ベンチャー企業で経営に近づけば近づくほど重要な力だと思っています」
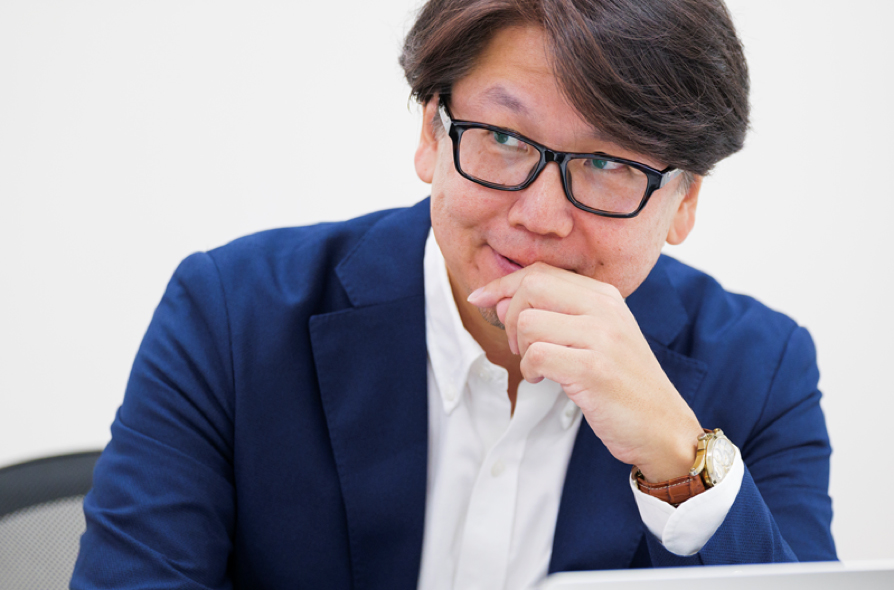
「知の帰属」へのこだわりは、ゴールにいち早くたどり着くため
「100年変わらなかった化学産業に、マイクロ波技術でイノベーションを起こす」。MWCCが掲げるビジョンを実現するには、すべてのクライアントが最短でゴールにたどり着ける道を示す必要がある。
そのために、MWCCがこだわっているのが「知の帰属」だ。MWCCと共同開発をする場合、プロセスと装置の知はMWCCに帰属する。技術プラットフォームやデータベースを蓄え、バックグラウンドIPとして活用することで、後続のクライアントの開発期間を短縮するためだ。MWCCは契約の段階でこの点を明確にし、納得が得られたクライアントとのみ開発に移行する。
ただし、例えばマイクロ波を活用したカーボンファイバーの開発では、ほかのクライアントのカーボンファイバーに関する開発に転用することはない。先行者利益を損なうことなく、マイクロ波を使った製造プロセスのグローバルスタンダード化を最短で目指していく。マーケットを作るという観点では、競合が出てくることも重要なのだ。
「多くの先行投資が必要で、かつスケールアップは難しいという共通認識が行き渡った分野ですから、当社と同時並行的にチャレンジする競合は出てきにくいと思っています。私たちは、マイクロ波による製造プロセスのパイオニアとなり、化学産業に変革を起こし世界を豊かにしたい。ぜひ、後に続く企業が出てきてほしいですね」
フィギュアスケートにおいて、かつては夢の技術だった3回転半ジャンプが一人の成功者によって急速に浸透したように、先駆者たるMWCCの成功がマイクロ波のハードルを一気に下げる可能性は高い。化学産業全体を変革する未来に向かって、MWCCは今日も「今できるジャンプ」の精度を粛々と高めている。
マイクロ波が叶える化学産業界のカーボンニュートラル。実績と今後の戦略│マイクロ波化学株式会社 後編 はこちら