Contents 目次
プロフィール
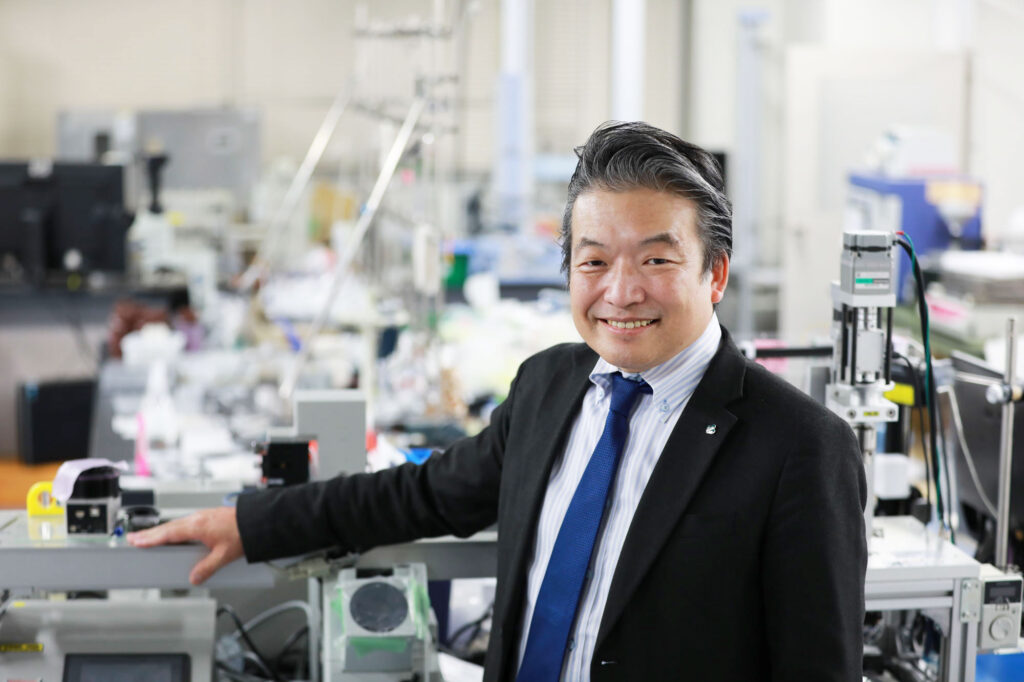
山形大学工学部機械システム工学科 教授 古川英光
フード·メディカル·ソフト材の3D/4Dプリンティング、ソフト&ウェットマター工学、ソフトマターロボティクスの社会実装を狙う高分子科学×機械工学研究者。東京工業大学物理学専攻博士課程修了、博士(理学)。東京工業大学助手、東京農工大学助手、北海道大学准教授を経て、2009年4月山形大学准教授(2012年より教授)に着任し「ソフト&ウェットマター工学研究室SWEL」を設立、代表に就任。2018年4月「やわらか3D共創コンソーシアム」を設立、会長に就任。高付加価値と持続性の創造をローカルからグローバルに展開する、やわらかサイエンティスト。
生命現象の探求や半導体産業も支えるゲル研究
基礎的な質問となりますが、ゲルとはどういう物質を指す言葉なのでしょうか。
液体と固体の中間の物質、あるいはその状態のことをゲルと呼びます。分子同士で構成するジャングルジムのような構造の中で、1nmから数100nmの小さな網目に液体が捉えられて動けなくなっているのです。水に限らず油や他の液体でも、流動性をなくして柔らかくなっている状態であればゲルと言えます。
歯や骨を除けば、私たち人間の体もゲルからできています。体組成計に乗ると体の水分量が60%前後と表示されますが、この大量の水分を体の構造によって保っているわけですね。細胞一つひとつが網目構造を成しているようなイメージです。さらに、その細胞自体も小さい膜の中にタンパク質や糖、DNAを含む細胞核や水がぎっしり詰まったゲルだと言えます。生命現象がゲルの中で起きているという事実は、ゲル研究の重要な意義を担っていると思います。
生命の起源に関わるものとしてゲルを捉えたことはなかったので、非常に興味深いです。日常生活や産業においては、どのようなシーンでゲルが利用されているのでしょうか。
わかりやすいのはソフトコンタクトレンズです。視力を調整するだけでなく、酸素の透過性を良くしたり、乾きにくくしたりと、精度の高いものづくりが実現しています。もともとは硬質のプラスチックで作るハードコンタクトレンズが主流でしたが、目に触れても刺激が少なく、割れる心配もないものとして、ゲルで作られたソフトコンタクトレンズが普及しました。医療分野では、人工血管や人工軟骨といったかたちでも活躍しています。
ゲルが持つ高い吸水性は、汗とりパッドや紙おむつでも活用されています。ゲルの種類によっては自重の1000倍もの水分を吸収できるので、たった1gの粉末を含ませるだけで1Lも吸水できます。ゲルが水分を取り込んだ状態で凍らせたものは、保冷剤としても利用されています。
工業においてもゲルは欠かせない存在です。ゲル分子の中にイオンを含ませると、水中のイオンを吸着して水を綺麗にする効果があります。半導体産業などではイオンのない脱イオン水が必要不可欠なので、イオン交換樹脂として用いられるゲルのニーズは根強いものです。他にも、リチウムイオン電池の性能向上や安全性の高い半固体電池(ゲルバッテリー)の開発のために使われています。
生命のメカニズム探求から工業に欠かせない素材まで、ゲルの研究は広い分野に波及していくのですね。
物や現象の性質を研究して、そのなかから共通性を探すのが物理学という学問です。ゲルにもさまざまな種類がありますが、その共通点がわかると、生命現象や食べ物、薬からコンタクトレンズまで同じ原理で説明できるようになります。物理学はコンピュータで言えばOSのようなもので、その上にさまざまな学問や個別の事象が上乗せされていく性質があると感じています。
大学院で研究を始めたての頃、先生が液体から実験用のゲルの塊を目の前で作ってくれたのですが、私にはそれが面白くて。物理学では実験用の素材を提供してもらうことが多いので、研究対象そのものから作ることが新鮮でした。緻密で神秘的な生命現象に思いを馳せる一方で、簡素化したモデルや原料を作って研究する、そうしたシンプルな屋台骨からのアプローチにも面白さも感じています。
ゲルの実用化を加速する3Dプリンター
現在古川教授は山形大学で3Dゲルプリンターの開発に取り組まれています。素材研究と機械開発は異なる領域かと思うのですが、どのような経緯があったのでしょうか。
かつてゲルは力学的強度に乏しく、膝軟骨のように負荷のかかる用途には利用できないという弱点がありました。しかし精力的な研究により、2000年前後に高強度のゲルが同時多発的に生まれたことで、人工軟骨や血管といった生体代替材料への応用への道も開かれていった歴史があります。
私も素材研究に携わるなかで、学会でゲルを紹介すると「その素材でこの形を作ってほしい」といったリクエストを受けるようになりました。あるとき要望を受けて膝の半月板を作ろうとしたのですが、なかなか難しくて。豚の半月板から起こした型を使ってみても、ゲルは液体を吸収して膨らむ性質(膨潤性)があるので、本来必要とされていたサイズよりも大きくなってしまい、素材を実用的な形にすることの難しさを感じました。
そうした経験も経て、研究者として、良い素材を社会の中で普及させたいという思いが強くなっていきました。そのためには、素材自体の研究だけでなく、世の中の人が使えるようなかたちで実用化させることも必要になります。実用に近づけるならものづくりを学ぶべきだという発想で、山形大学工学部に移ったのです。
そこで初めてCNC加工装置を目にしました。XYZの座標指定に従って刃物が回転し、金属の塊を削り出すというものづくりの現場を目の当たりにしたわけです。それからしばらく経ったある日、学生と食堂で話している時に「刃物の代わりに、ゲルを反応させるための光ファイバーを動かして、液体の固めたいところだけに照射すればいいのではないか?」と思いついたんです。
今につながる、3Dゲルプリンターの原型ですね。
「3次元上を動いて印刷するから『3Dプリンター』だね」なんて話をしていたのですが、世の中には既に3Dプリンターと呼ばれる機械があることを後から知りました。デジタル空間上ではサイズの変換が簡単にできますから、半月板づくりで直面したような問題が解決できるんです。3Dプリンターによって、あらかじめデータ上でサイズを調整したゲルを造形できるようになったことは、とても大きなメリットでした。
現在古川研究室で扱っている3Dプリンターの方式について教えていただけますか?
大きく分けて2種類のプリンターを開発しています。素材をペースト状にして、押し出しながら積層していく方式の3Dプリンターは、食品の3Dプリントで活用してきました。素材ごとに色や味が変わり、目でも楽しめるものが作れます。
もう一つの方式は、バットに入れた液体を紫外線やレーザーで固めながら積層していく「バスタブ方式」と呼んでいるものです。ゲル化剤が含まれた液体や、食品の粉が含まれたでんぷん分散液にレーザーを当てることで、硬化された部分だけをゲルとして取り出せるようになります。手作業では難しい細かなパターンや、中空構造なども造形でき、場所ごとに透過率や硬さを変えることも可能です。
研究室の外でも3Dゲルプリンターが活躍する機会を設けていますよね。2022年に渋谷で行われたイベント「やわらか記念写真」では、今まで写真や映像では残せなかった「やわらかさ」を3Dプリンターで再現し、残すという取り組みが印象的でした。
実は「やわらか記念写真」の企画初期段階では、造形に6時間もかかっていました。イベントとしてどう成り立たせるか悩んでいたのですが、関係者で話して、3Dプリンターを一から設計し直すことに決めました。オープンソースで設計図が公開されている3Dプリンターをベースに開発し直したところ、造形時間を30分にまで短縮できたんです。
すさまじい高速化ですね。
初めは難しい仕組みや装置を使っていましたが、最終的にはシンプルで手に入れやすい部品で作ることに辿り着きました。ゲルを固めるためのレーザーも、自分で3Dプリンターを作り始めた頃には、1000万円以上もする研究用途のものを使っていたんです。物理学の世界ではスタンダードな装置でしたが、その結果3Dプリンターが高額で扱いも難しくなってしまうと、あまり欲しいとは思えませんよね。今思えば、自分が学問の世界で見てきた常識に縛られていたようにも思います。
イベントで使った3Dゲルプリンター「GelPiper mini」のレーザーには、ブルーレイディスク用に市販されている数万円程度の部品が採用されています。当たり前の構造や機材を疑って、オープンソースの設計を取り入れたり、全く異なる部品を使ってみたり。技術が本当に使われるよう進化するためには、自分たち自身でちゃぶ台返しをするような、質的な変換やイノベーションが必要なのだと思った出来事でした。
技術を社会に普及させるためには、これまでの常識にとらわれないような考え方の変化が必要なのですね。
最近、シャープで電卓を発明した佐々木正さんの本を読みました。電卓も最初は500万円もする装置でしたが、佐々木さんは最初から八百屋さんが胸ポケットに入れて使うことを夢見ていたそうです。小型化するために、液晶を採用したり、太陽電池で動くようにしたりと、扱う技術もどんどん変換されていきました。誰もが使えるものにしたいという夢があったからこそ、技術や手法にとらわれずにいたのだと思います。技術を社会に普及させるためには、こうしたチャレンジを続けるほかないのだと強く感じました。
研究の知見を共有し、新たなアウトプットを生み出すコンソーシアム
3Dゲルプリンターを用いて商品化された事例も生まれていますよね。
高強度ゲルで作った「月のクラゲ」が商品化されました。クラゲの動きや質感を再現したゲルクラゲを水槽の中で漂わせるもので、家庭やお店で人を癒すような役割や、テレビのセットの一部としても使われています。
最初は海に浮かべるクラゲ型のロボットを想定して作り始めたのですが、鶴岡の加茂水族館の館長さんに開発中のゲルクラゲを見せたらとても好評で。また、ゲルクラゲについて講演で話していたら、山形に本社を置くNDソフトウェアの方も製品化やセールスに協力してくれました。さまざまな方の支援を受けた「月のクラゲ」のクラウドファンディングは、あっという間に目標金額を達成しました。
私が当初想定していたゲルを用いた人工半月板のようなアウトプットと「月のクラゲ」では、全く性質が異なります。ニーズは他の人が発見してくれるものだと思いましたし、売る人がいなければ広まらないことも実感しました。
他の企業や専門家とコラボレーションすることで、思いもよらないアウトプットに繋がったのですね。
電通、デンソーウェーブ、東北新社と取り組んだ「転送寿司(スシ・テレポーテーション)」のプロジェクトも印象的でした。純粋な物理学者のメンタリティであれば、素朴でも動作すれば良いと思いがちです。しかし、ロボットアームで寿司を組み立てたり、グラフィックや映像の見せ方にも力を入れたりと、新しい発想を取り入れたことで、対外的に大きな反響を呼びました。
自分だけができることの範疇を超え、いろいろな道のプロや思いを持つ人と連携すれば良い物ができることを実感し、共創という言葉を意識し始めました。3Dゲルプリンターを普及させたい私にとって、それを用いて何を作るかという観点は重要かつ、他の方や力添えなしには得られない要素だと思います。

東京から寿司のデータを転送し、米国のイベント会場で出力する――そんな「SUSHI TELEPORTATION」を目指すプロジェクトチームが食感や味などのデータを基に、1辺が5ミリの食べられる立方体(ゲルキューブ)をロボットが組み立て“低解像度のピクセル寿司”を再現した取組。
YouTube:https://www.youtube.com/watch?v=WwvgsMRuRPs
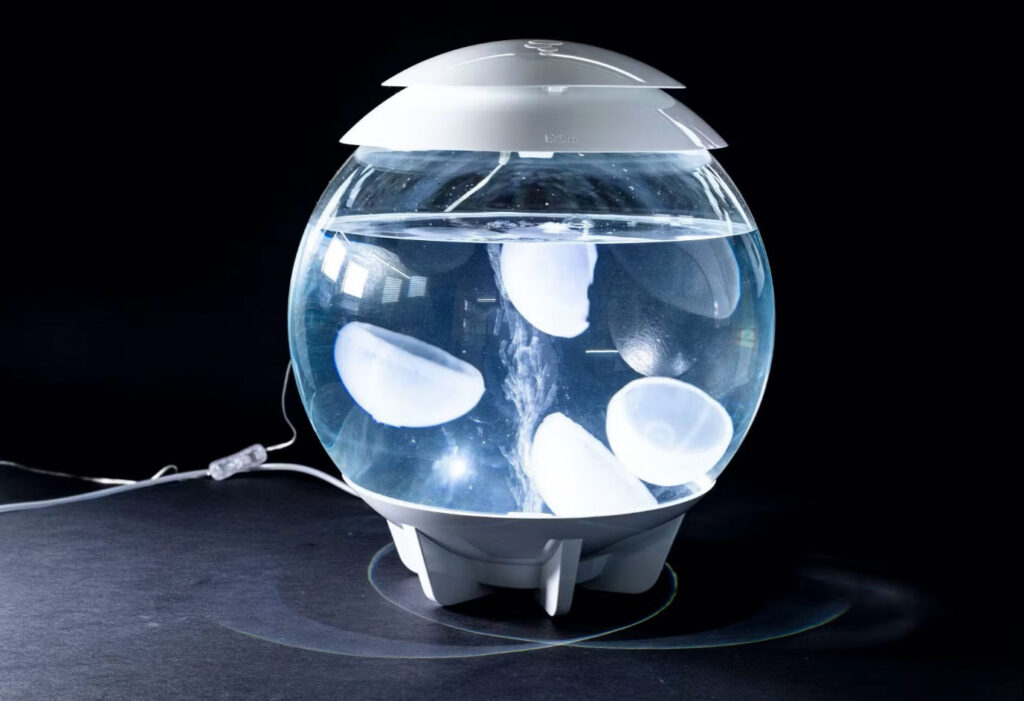
2018年4月から始まった「やわらか3D共創コンソーシアム」は、まさに産学官民を超えた連携を生むためのプラットフォームかと思います。設立の経緯や活動内容を教えてください。
3Dプリンターの開発が進むにつれて、研究室に関心を持ってくれる方が増えていきました。研究室でマネジメントできる数には上限もありますから、一対一で接するだけでなく、大勢で集まって知見の共有やコミュニケーションを行うコンソーシアムを作ることになりました。
研究室に寄せられる相談には、高強度ゲルを事業化したい、電池の性能向上にゲルを用いたいといった具体的な技術に対するアプローチだけでなく、まずは一度話を聞いてみたいといった声も多かったのです。関心が共通する部分はオープンに共有しながら、大学と企業間でクローズに行う研究も並行する、オープン・クローズドの概念を設計して運用しています。
最初は24団体ほど、今では30近くの団体に参画いただいています。コンソーシアムで新しく関わりができた企業の多くは食品業界が中心で、私を応援する声を直接聞く機会もあり、とても感動しました。3Dフードプリンターはまだ歩き始めの技術なので、現時点で各社がしのぎを削るのではなく、まずはコンソーシアム内で知識を共有して、そこから良いトピックを探していけるような方式にしています。
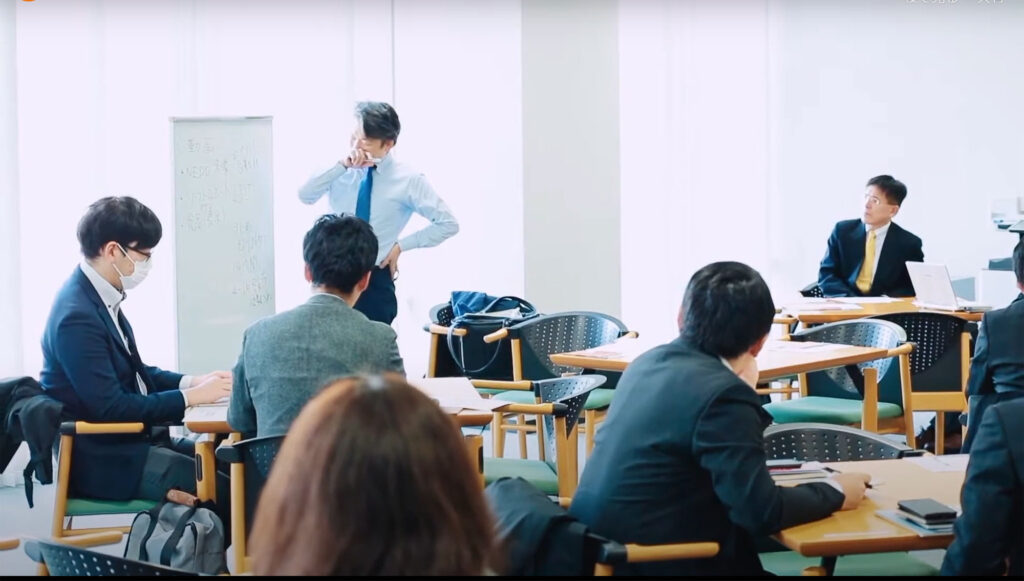
柔らかな3Dプリントが社会に浸透する未来
古川教授が思い描く未来では、ゲルや3Dプリンターはどのように活躍しているでしょうか。
フードプリンターの開発で意識しているのは、日本人を「調理する」という家事から解放することです。手作りの食事を届けるのは大切ですが、こだわるあまり負担が大きくなっては本末転倒です。
また、食品ロスを解決することにも取り組んでいます。世の中には、形や見栄えが悪いだけで市場に出回らない野菜や果物がたくさんあります。3Dプリンターは食材を粉末やペーストにして扱うので、形の良し悪しが関係なくなるため、農家の方も収穫量を上げられますよね。買い込んだ食材を使いきれないという問題も、3Dプリント用のインクや粉末として食材の長期保存が可能になれば解決に近付きます。
いずれフードプリンターは小型化して、「スマート弁当箱」として持ち歩けるようにしたいと考えています。手で持ち運べるようになり、空気中から水分を取り入れる技術や、太陽光発電なども組み合わせれば、どんな場所でも食べる物について心配する必要がなくなりますよね。テクノロジーで人間が生き延びることを支え、さらに楽しい面が最大化されるように研究を続けていきたいと思います。
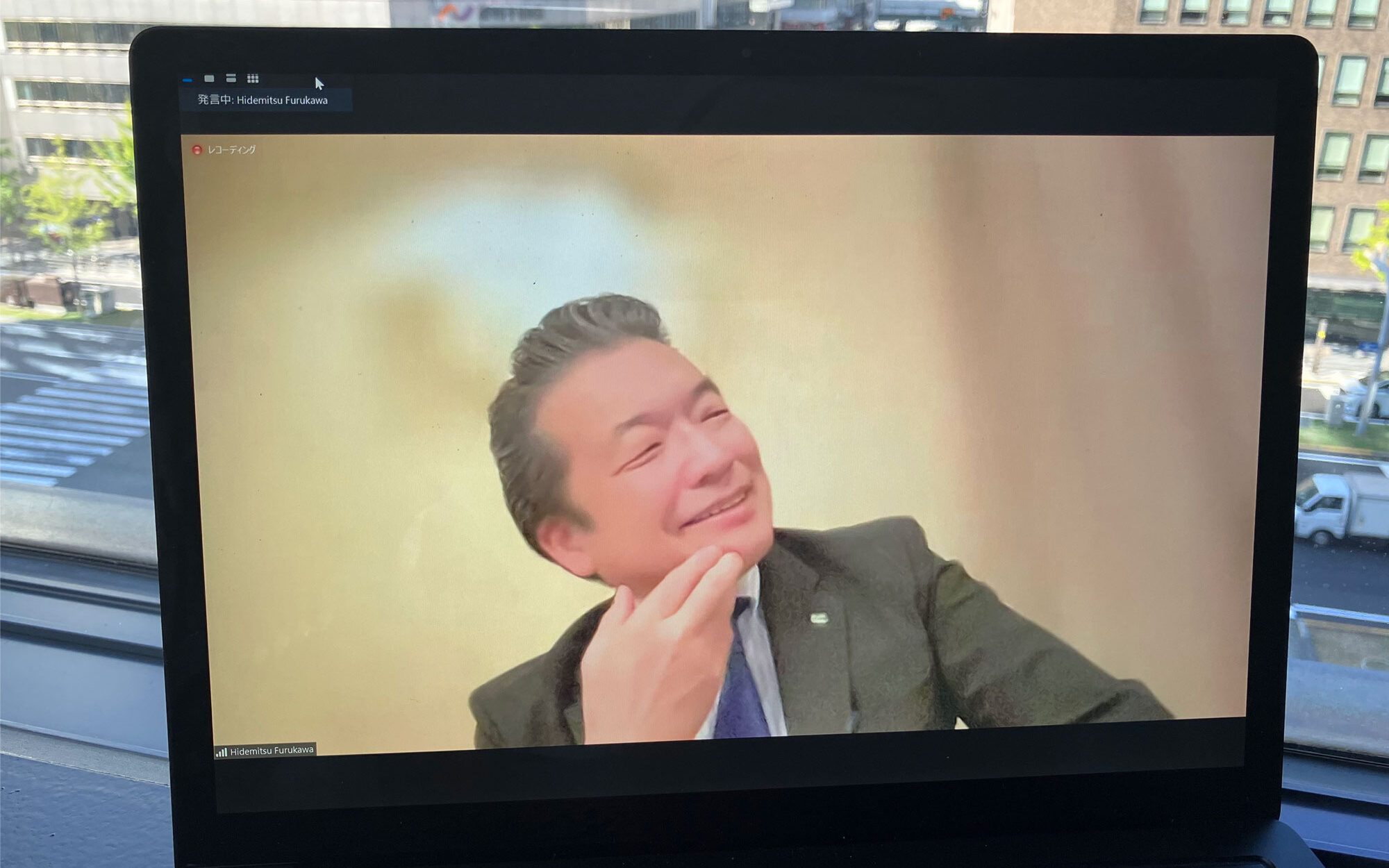
「スマート弁当箱」が当たり前になる未来が楽しみです。食以外の分野でも3Dプリンターは活躍しそうですよね。
そうですね。やわらか3D共創コンソーシアムでは、ゲルの基本的な研究の他に、食品・医療・モビリティ・ロボットの部会を設けています。そうした各分野での応用や、建築用3Dプリンターのように大きな装置の開発なども含めて、柔らかい3Dプリントが活躍する可能性は大きいでしょう。
コンソーシアムでは「材料 “30年” を、材料 “3ヶ月” に」という言葉を掲げています。日本の強みである材料開発を、いち早く現場で活躍させるため、3Dプリンターを開発してきました。今は3Dプリント後のゲルの変形も含めて設計する「4Dシミュレーター」の開発にも取り組んでおり、さらなる素材実用の高速化を目指しています。
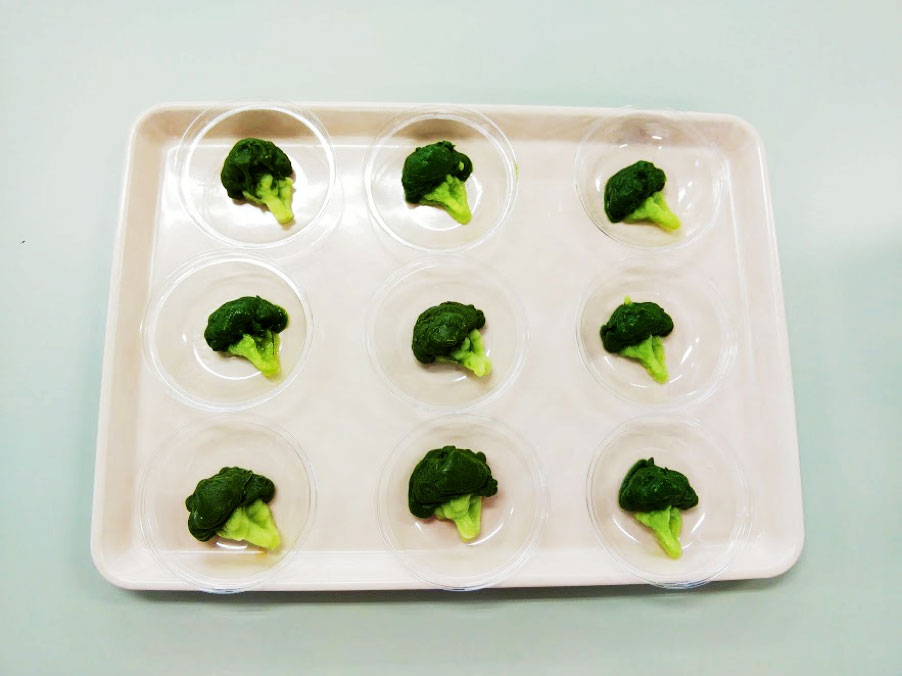
(2023年6月22日に実施)