Contents 目次
プロフィール
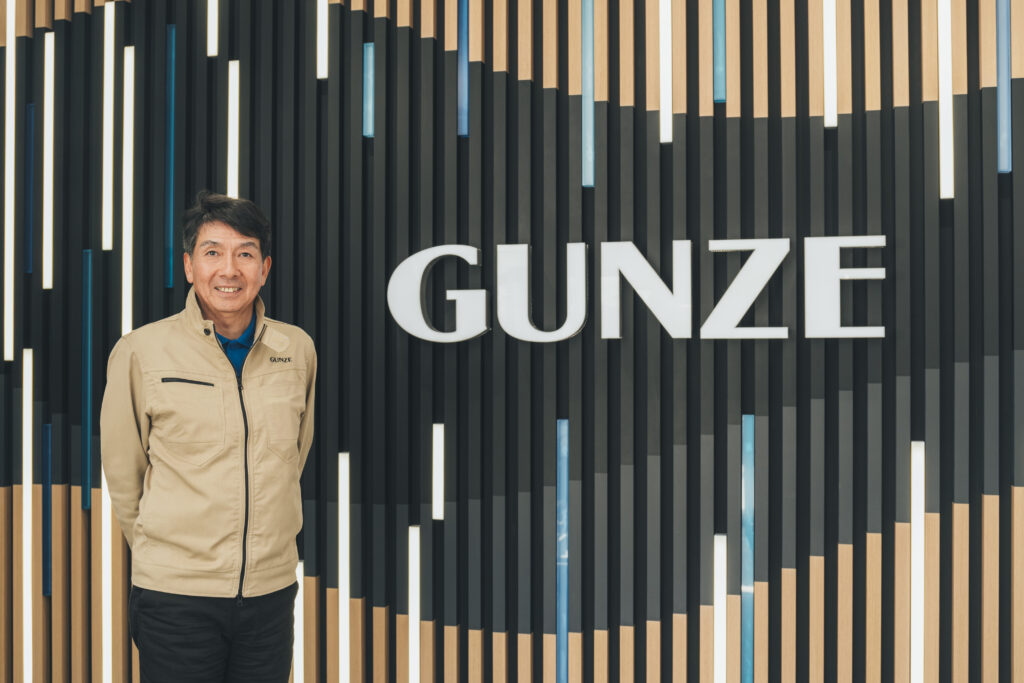
グンゼ株式会社執行役員プラスチックカンパニー長 花岡 裕史(はなおか ゆうじ)さん
1988年グンゼ株式会社入社し、プラスチック部門にて、主に収縮フィルムの営業開発、商品開発、生産技術を担当。ベルギー、中国での勤務を経て、2017年営業統括部長就任、2019年技術部長および守山工場長就任。2022年4月執行役員 プラスチックカンパニー長に就任、現在に至る。
サーキュラーファクトリー挑戦へのはじまり
グンゼは2023年4月18日、プラスチックフィルム事業の基幹である滋賀県守山市内の守山工場の敷地内に、鉄骨造、延床面積10,786m₂新製造棟を竣工、「サーキュラーファクトリー(資源循環型工場)」に転換した。同製造棟は守山工場敷地内の太陽光や水資源をエネルギーとして活用していく他、2030年までにプラスチック廃材を出さないゼロ・エミッション実現を目指す。さらに食品包装向けに自社で製造する異種積層されたフィルム廃材を回収し、異種分離および再生技術を確立しながら、100%循環型原料を使用した製品づくりにも取り組んでいく。
グンゼは2019年12月に、プラスチック資源循環基本方針を制定。プラスチックの廃棄量削減と、プラスチック資源が循環する社会の実現への貢献を宣言した。プラスチックフィルム事業においては、2027年までに使用原料の50%をリサイクルおよびバイオマスなど循環型原料に置き換え、2030年には100%まで引き上げるとしている。
その背景には、国際的規模で問題となっているプラスチックによる環境汚染がある。国内においてもプラスチック資源循環を推進するため2019年「プラスチック資源循環戦略」が策定された。世界のプラスチック生産量は増加し続けており、1950年以降生産されたプラスチックは83億トンを超え、63億トンがごみとして廃棄され、毎年約800万トンが海洋にゴミとして流出しているという報告がある。そして、廃棄の多くを占めているのがボトルや包材類だと言われる。生活用品ボトルや食品用の容器や包材などの多くが使い捨での使用となるためだ。日本の人口1人当たりのプラスチック容器包装の廃棄量は世界第2位とされており課題は大きい。
「弊社は食品の包装資材をメインに扱っていたので、非常に危機感を感じました。しかし、プラスチックが悪なのではなく、捨てられてゴミとなるから悪になるのです。回収し、再資源化して循環する仕組みを作れれば、環境に優しい素材となり得ます。
プラスチックは瓶や缶に比べて低温成形できるので、エネルギー消費も少ない。さらに(缶と瓶と比較して)軽量でありながら丈夫であるため輸送コストも抑えられる。結果的にCO₂排出の抑制にもつながる素材です」(花岡氏)。
ならば、どうやってプラスチックを循環させるか――グンゼの答えが、守山サーキュラーファクトリーでの取り組みだ。
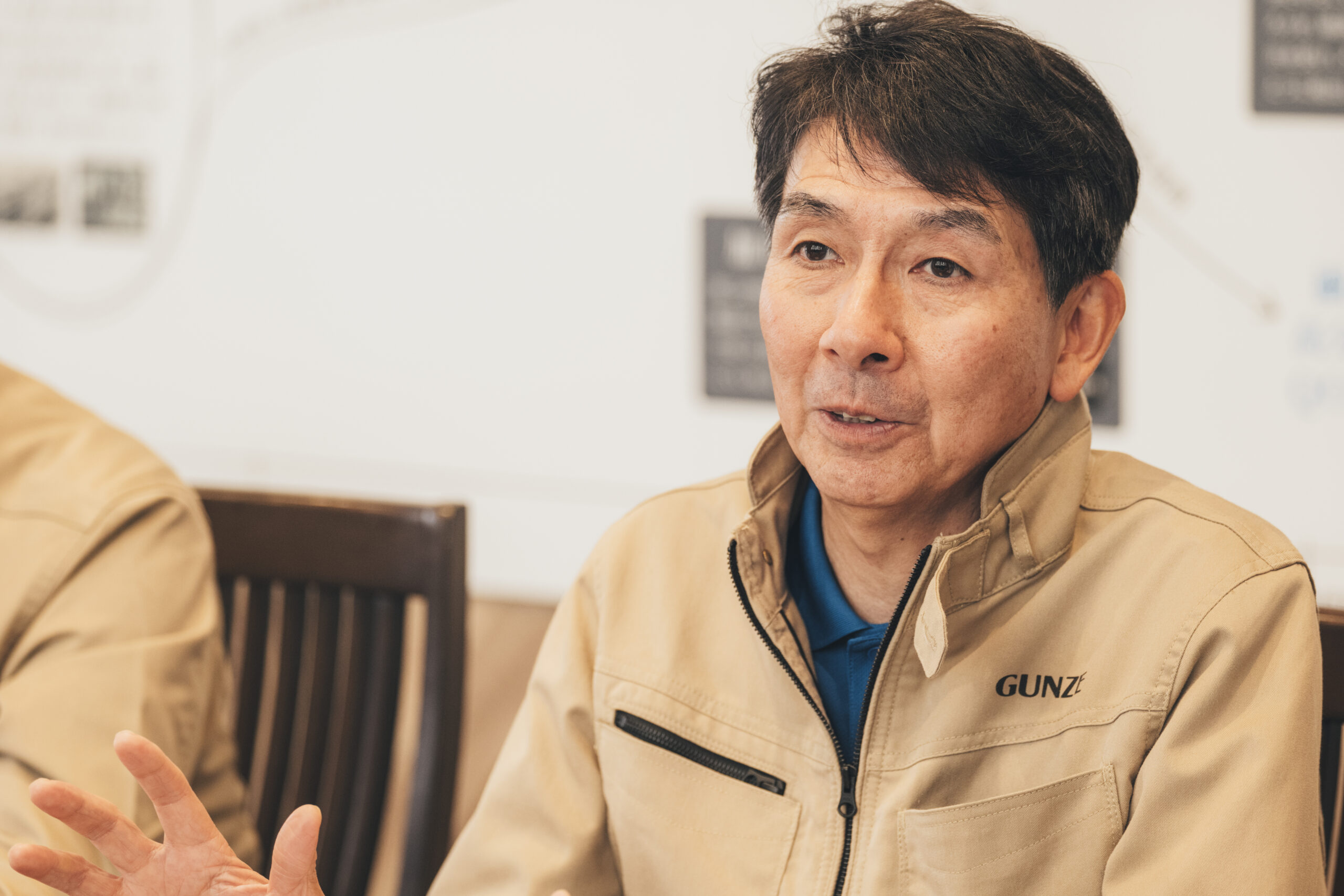
2024年までに「ごみゼロ」達成は確実に。製造ロスを再資源化し、廃棄ゼロへ
サーキュラーファクトリーでは、工場内の産業廃棄物(生産中に発生する端材などの廃棄ゴミ)を再生利用するポストインダストリアルリサイクル(PIR)から取り組み、2030年までに市場から回収される使用済み製品から再生を可能とするポストコンシューマーリサイクル(PCR)の実現を目指していく。
その第1歩として同社が目下取り組むのが「ごみゼロ」だ。グンゼは下記の3ステップをロードマップとして設けている。
- 2024年度末までに守山工場における「ごみゼロ」達成
- 2027年までに海外拠点「ごみゼロ」達成
- 2030年までにグループ全体での「ごみゼロ」達成
守山工場では主にペットボトルや洗剤容器のラベルに使用する収縮フィルムを生産。「ごみゼロ」に向け、まず製造過程での廃プラを削減し、その上で生じる廃プラは回収して再原料化し活用する。こうした一連の取り組みを通じ「工場からごみを出さない」環境、廃棄物の発生をなるべく抑制する生産設備への改善・設計に取り組んでいる最中だ。
取り組み事例には、フィルムを所定の幅に切断する際に生じる材料ロス、いわゆる「耳ロス」の再利用がある。これを”ゴミ”にせず”材料”と捉え、回収と再利用のサイクルを地道に回す。
生産中の異常によりフィルムが切れてしまった場合、従来は人が急いで駆けつけて2人がかりで回収を行っていたが、新工場ではオリジナルの自動仮巻き装置を導入。自動で余分な部分を切り落とし運搬も簡易となった。
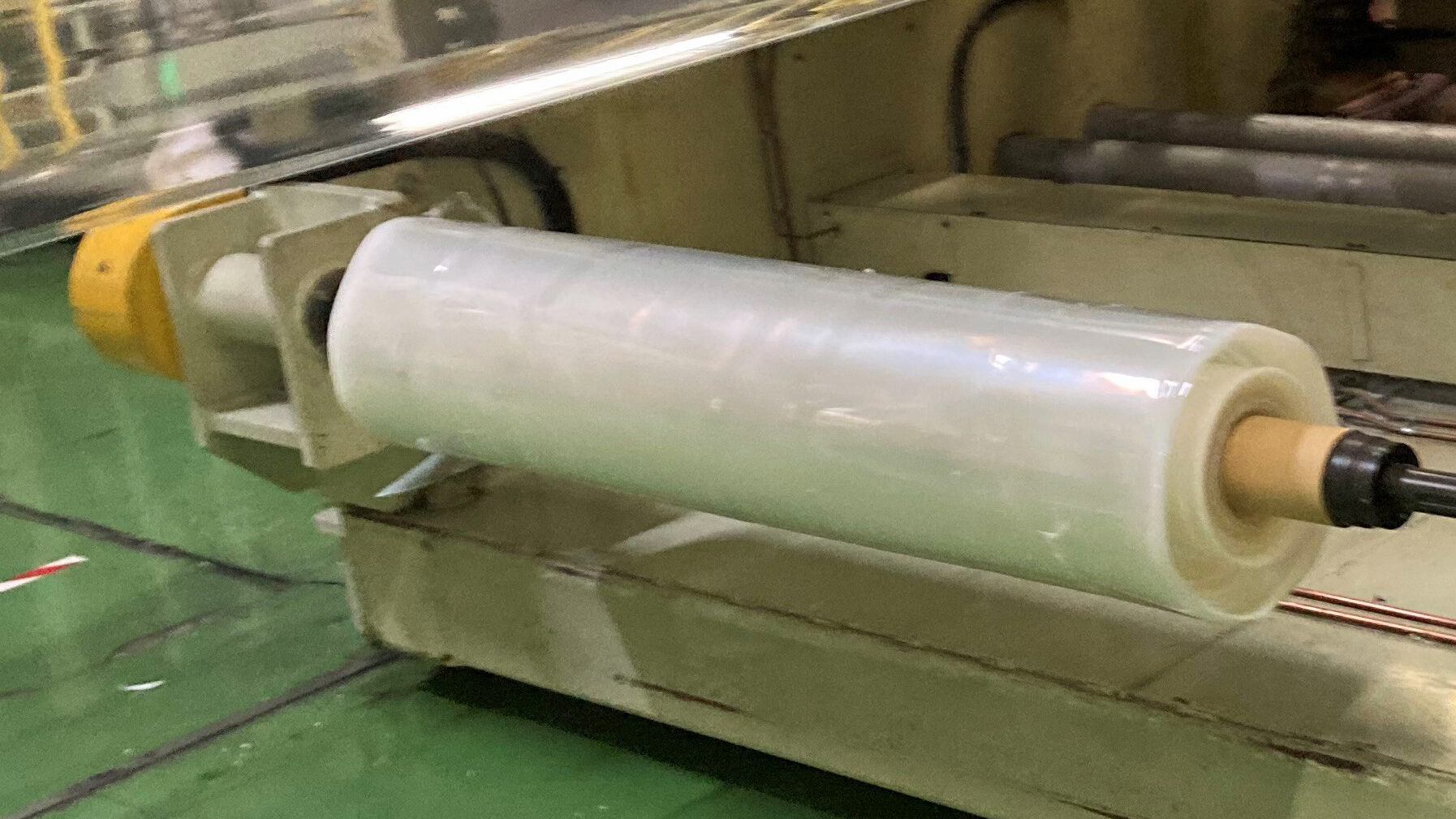
圧縮された”フィルム屑”や押出成形機から排出される比較的大きな塊の”樹脂ダンゴ”の処理手段に課題をかかえていた。そこで、リサイクルセンター内に大型粉砕機を導入し、形状の異なる樹脂を破砕・粉砕し、マテリアルリサイクルさせる。この設備は、1台で年間130トンの加工が可能であり、今後の削減に大きく貢献する見込みとのことだ。
グンゼのフィルム関連のリサイクルの現状としては材料物性の要求条件が厳しい半導体用フィルムは、食品フィルムのように水平リサイクルが難しく、副資材などに再生する可能性が高いという。
「5年程前の守山工場全体のプラ産業廃棄物は1200トンほどでしたが、現在はそこから500トンまで削減できています。近いうちにマテリアルリサイクルで100~150トンまで削減した上、残りについては、パレットや社内アパレル部門で使用するボビンへのリサイクルを行い、汚れ等でどうしても再活用できないものをサーマルリサイクルで運用することでゼロにしていきます」と2024年までの守山工場における「ごみゼロ」達成は見えていると説明する。
100~150トンという数字は、一見『多い』と感じるかもしれないが、守山工場全体の年間プラスチック製品生産量は約1万数千トンにのぼるため、発生量としては1%を切る数字だ。
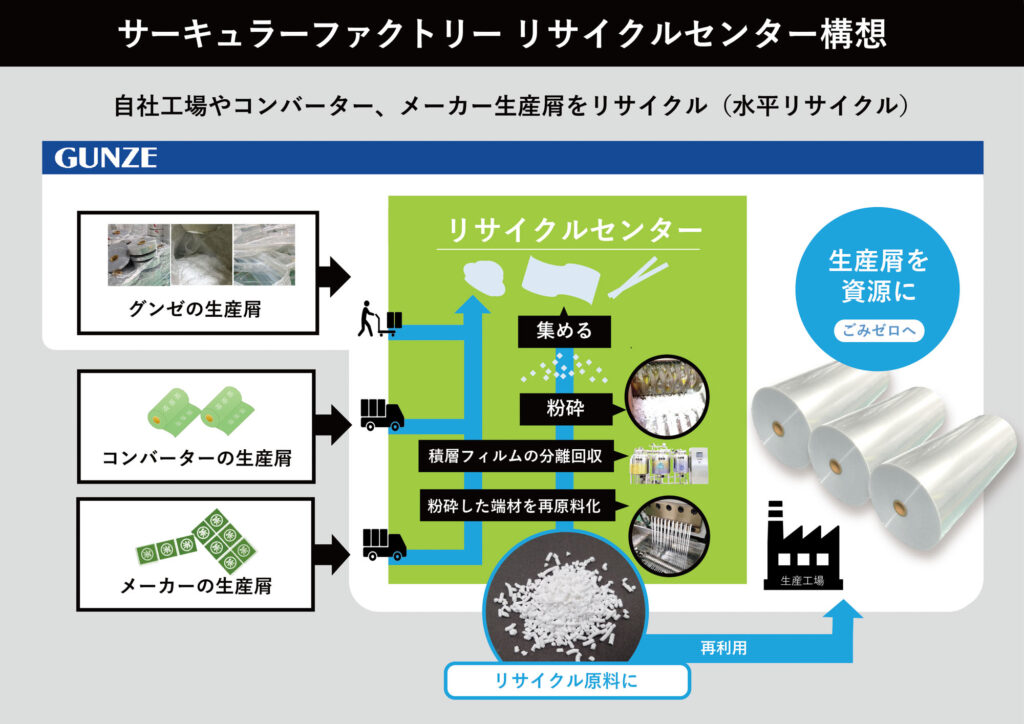
生産効率の最大化を図るモデル工場に向けて。進化する環境をつくる人材を育成
守山サーキュラーファクトリーは、「資源(Material)、機械・設備(Machine)、人(Man)」の3つのMを循環させながら発展する工場をコンセプトとして掲げる。
建屋の屋根全体に太陽光パネルを配置し、受光面積を広く取ることで発電量を高めている他、建屋の中は日陰となるため空調負荷を抑えることが可能なり、年間CO2削減量446t-CO2を見込む。また、琵琶湖から車で約15分の立地を活かし、豊富な地下水を機械の冷却や空調に活用。それにより温まった地下水を暖房の補助熱源として活用し、二巡させ、温度を下げた状態で戻す設計がなされている。
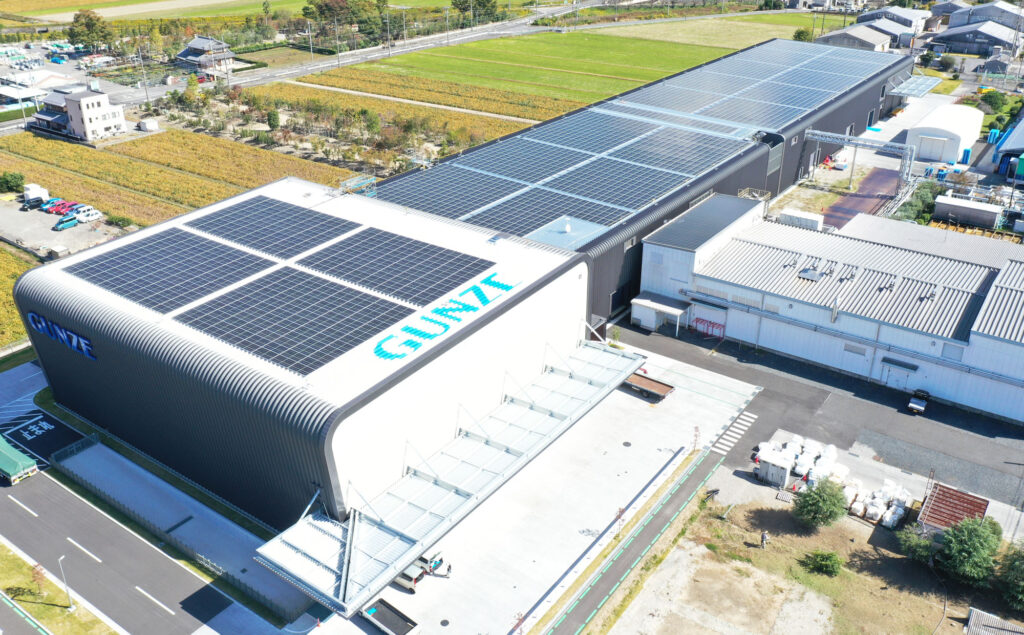
新工場は、機械・設備(Machine)により製造工程が自働化・機械化されており「実質無人化」を実現している。
従来30人以上が配置されていたラインが、一部軽作業を除くが、中央管理室から1人で制御することが可能となった。以前は熟練のオペレーターが、100項目以上のフィルム条件出しの設定を行い、原料の運搬、パレットの片づけ、数量管理、原料の入れ替え、検品や最終製品の梱包など多くの作業が人の手で行われていた。
機械化は重量物や熱、裁断など危険な作業から人を解放するだけでなく、人の経験によるカンも数値化できる。さらに、システムに落とし込むことで、標準化を進め品質の安定化にも貢献する。工場全体の生産管理を集約して行うことで製造ロスや材料の無駄をなくし、生産性やエネルギー効率も向上するなど全体最適につながっていくと言う。
同工場ではカーボンフットプリント(CFP)の可視化も進めており、新工場竣工前のCO2削減のシミュレーションでは、地下水の熱循環や再生可能エネルギーの利用、新規の生産ライン使用による生産効率向上を想定した削減可能な電気代(エネルギー代)を算出する。実績として見えてくるのは、稼働後ということではあるが、同社の新工場竣工前におけるシミュレーションでは従来の工場設備と比較して新工場では電気代が約7%削減できると試算している。
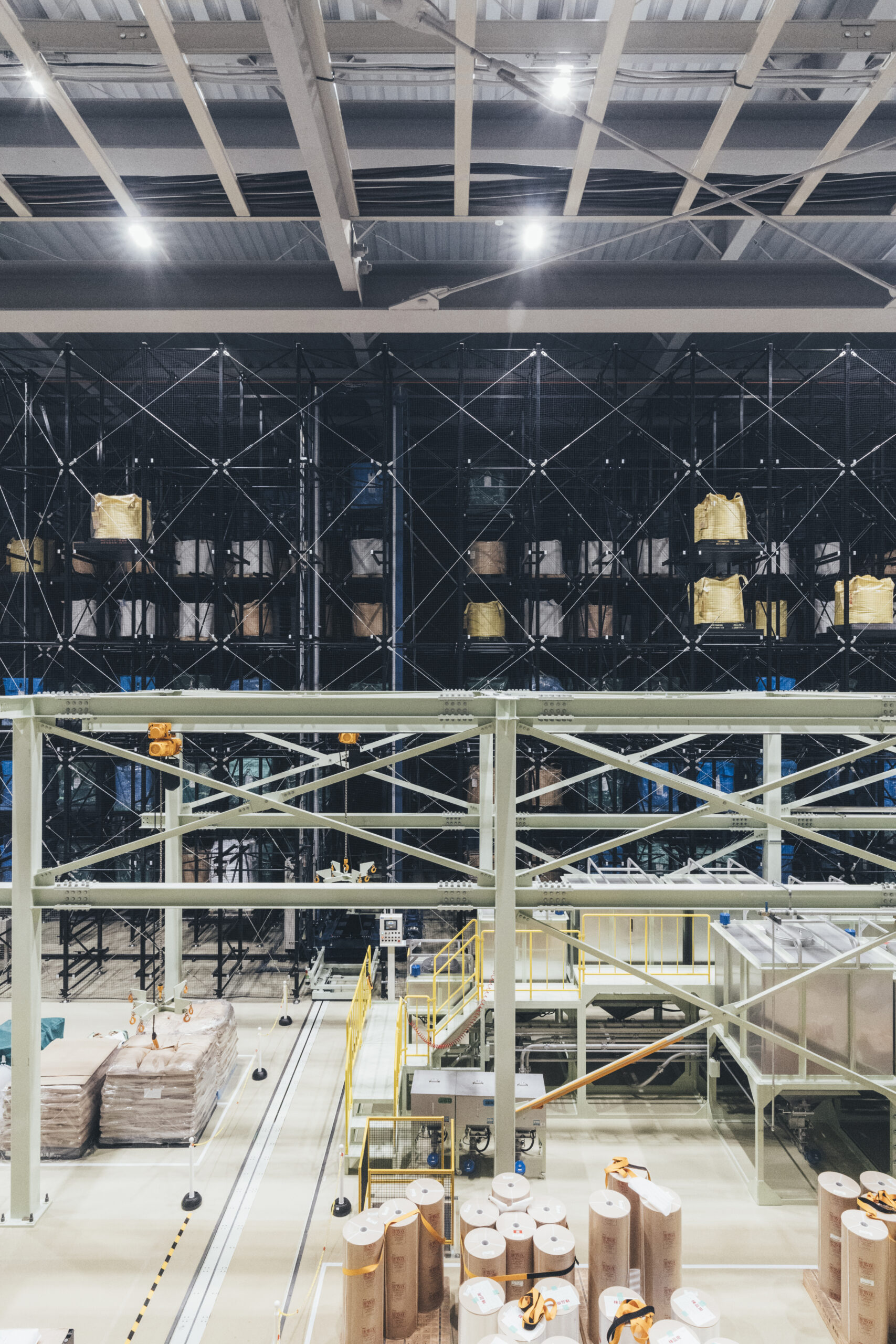
サーキュラーファクトリーで重要になってくるのが、機械化により設備総合効率を最大化し、省人化を実現することで、働く人をさらなる改善活動を行う頭脳集団に育成することだ。
省人化は『人を減らす』という意味ではなく、働き方を変えて人材育成を進めること。デジタル化によって創出された時間を、さらなる改善活動に充ててもらい、進化する循環を作って欲しいと想いを述べる。現状、守山工場では80人が24時間体制で交代勤務を行っているが、人の作業を極力なくし、将来的には夜勤をなくして働き方も変えていきたいと製造業の共通テーマともいえる「人手不足の深刻化」の課題へも切り込む意欲を示す。
守山工場での取り組みや技術は、同様に収縮フィルムを製造する海外三拠点にも横展開が進んでいる。海外拠点のリーダーに1~2週間滞在してもらいながら取り組みを共有。現在はそれぞれの拠点での展開を進めている。毎月、ごみゼロ会議をオンラインで実施。海外も含め40~50人のメンバーが集まり、各工場の推進状況や課題など全体での情報共有に力を入れる。
「プラスチックカンパニー全構成員のベクトルを合わせるために、当初は日本中の拠点を回り説明を行ってきました。今でも、個別にブレイクダウンした説明を繰り返しています」と花岡氏は述べる。
ゼロ・エミッション実現に向けて、着実に歩みを進めるサーキュラーファクトリー。資源循環だけでなく、機械化や省人化により人材育成も循環させながら、さらなる発展を目指す。後編では、グンゼの事業変遷や企業理念を通し、グンゼが目指す社会像を深堀する。
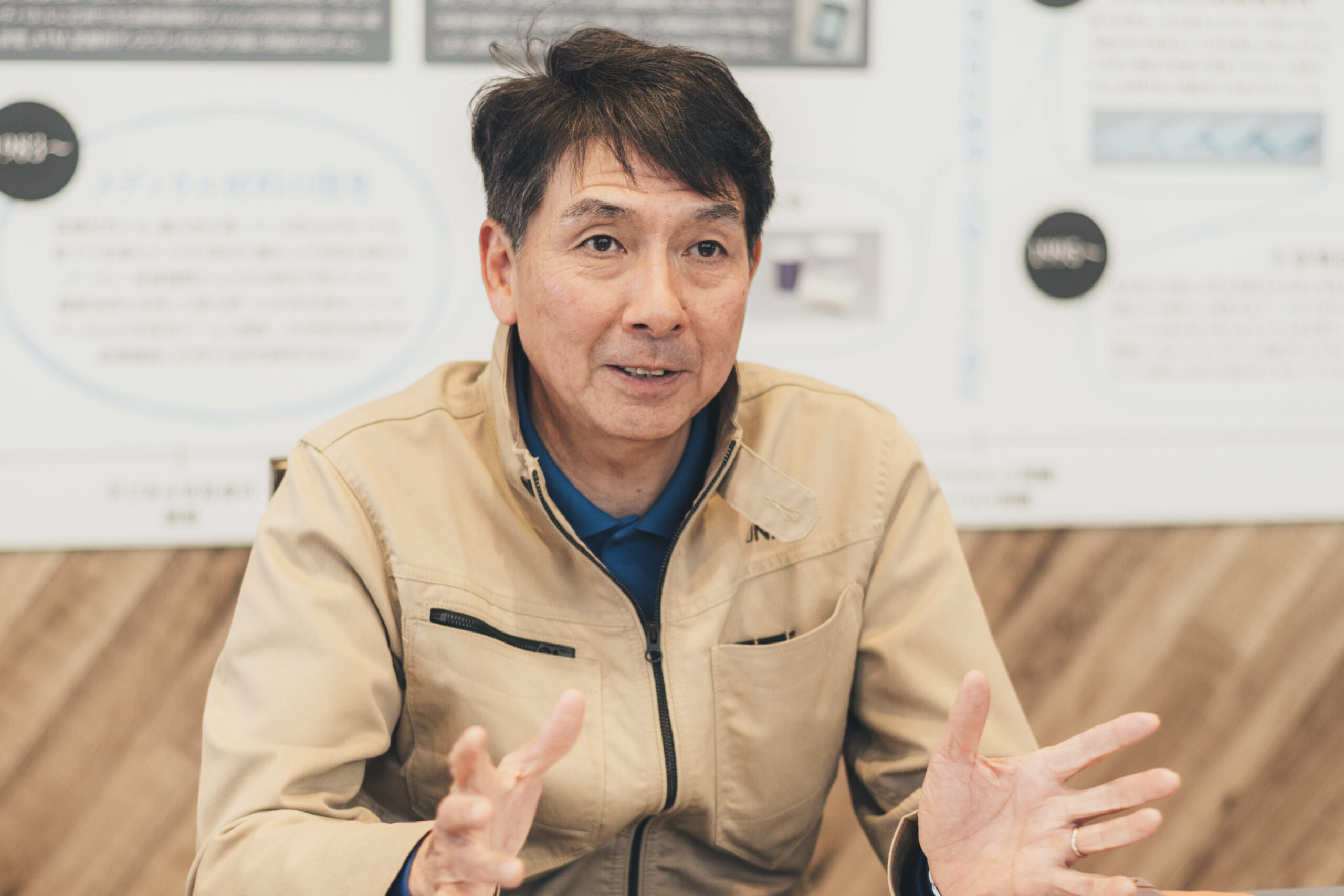
【後編】「資源循環」という神輿を担ぐ――バランスが重要なサステナブルな取り組み はこちら