Contents 目次
PVDコーティングとは
PVDコーティング(Physical Vapor Deposition /物理蒸着)とは、材料の表面に薄膜を形成する技術です。そもそもコーティングとは、金属などの加工対象の表面に処理を施し、何らかの特性を変えたり、加えたりすることで、蒸着とは、物質を高温に熱して蒸発させ、対象物に付着させて薄膜を形成することです。
PVDコーティングにより、対象の耐摩耗性、耐腐食性、硬度の向上などを大きく向上させることができます。
【PVDコーティングの主な事例・用途】
- 工具へのチタン(Ti)合金の蒸着
- スナック菓子等の内袋へのアルミ蒸着
- 精度の高い加工が求められる工具など
- 低温環境で使われる工具など
- 高硬度が必要な工具など
また、コーティングには物理蒸着(PVD)以外にも、「化学蒸着(CVD)」という方法があります。CVD(Chemical Vapor Deposition)は、複数のガスを反応させて膜を形成する技術です。通常、高温(800℃~1000℃)で行われ、最近では低温での成膜技術も進展しています。CVDで形成された膜は、均一かつ密着性に優れています。
【CVDコーティングの主な事例・用途】
- 半導体や工具へのチタン(Ti)合金の蒸着
- 耐久性の高さが求められる切削工具など
- 高温環境で使われる工具など
PVDコーティングの加工方法の種類
PVDコーティングの加工方法には、以下のような種類があります。
- 真空蒸着
- スパッタリング
- イオンプレーティング
真空蒸着
真空蒸着は、材料を真空中(10〜2Pa以下)で加熱し、蒸発させた蒸気を基板上に凝縮させて薄膜を形成します。真空状態にすることで、材料の気化温度が下がり、1,000度ほどで気化させることが可能です。
真空蒸着では、まず素材の表面に付いているホコリなどを除電ブローで取り除き、密着を良くするためにアンダーコートを事前に行います。蒸着後は、表面を保護するためにトップコート塗装を施し、最後に外観検査を行います。
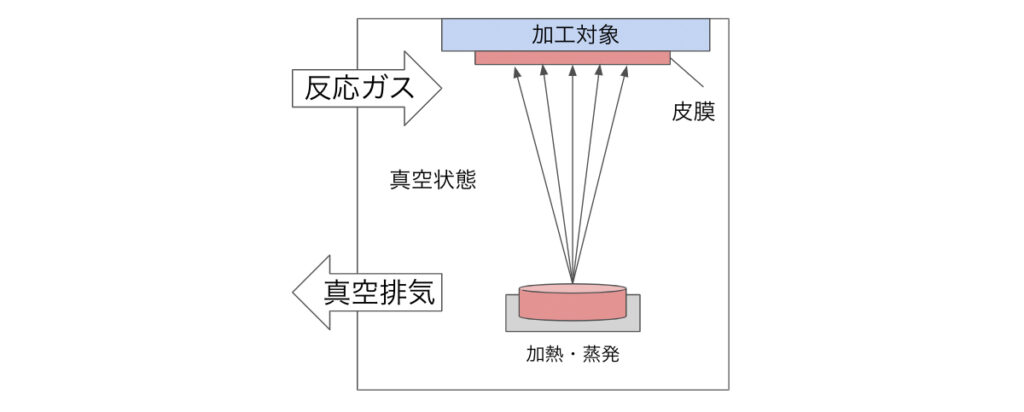
メリット | デメリット |
|
|
真空蒸着は、上記で挙げたメリット以外にも、処理温度が低いために加工対象へのダメージを抑えられる利点があります。一方、デメリットとしては、シンプルな機構ゆえに蒸発粒子のエネルギーが低く、密着性が高くない点です。
スパッタリング
スパッタリングは、活性ガス(アルゴンなど)をイオン化して衝突させることで、材料の分子・原子を放出させ、それを加工対象に付着させます。
最も一般的な「2極スパッタリング法」や、成膜スピードを高めた「マグネトロンスパッタリング法」、導電体向けの「DC(直流)スパッタリング」といった方法があります。
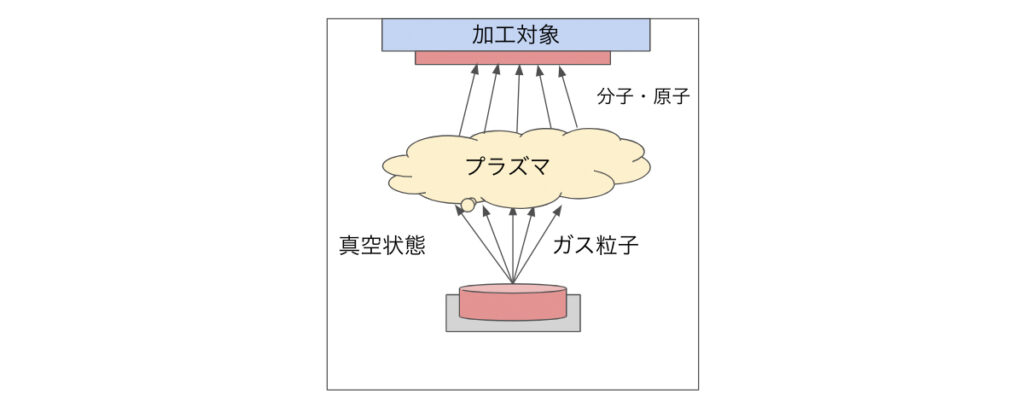
メリット | デメリット |
|
|
スパッタリングのメリットは、付着力が高く、高い制御性を持つことです。また、蒸着で難しいSUSやニッケルクロム合金などに対応できます。一方で、設備が複雑で高価なため、導入コストが高くなることがあります。
イオンプレーティング
イオンプレーティングは、真空中で蒸発したガスをプラズマ中にイオン化し、製品にぶつけて成膜するものです。簡単に言えば、真空蒸着にプラズマを加えています。
電子ビームガンを用いる「中空陰極放電法」や、アーク放電を引き起こす「アーク放電法」は、チタンやクロムなどの成膜に用いられることが多いです。
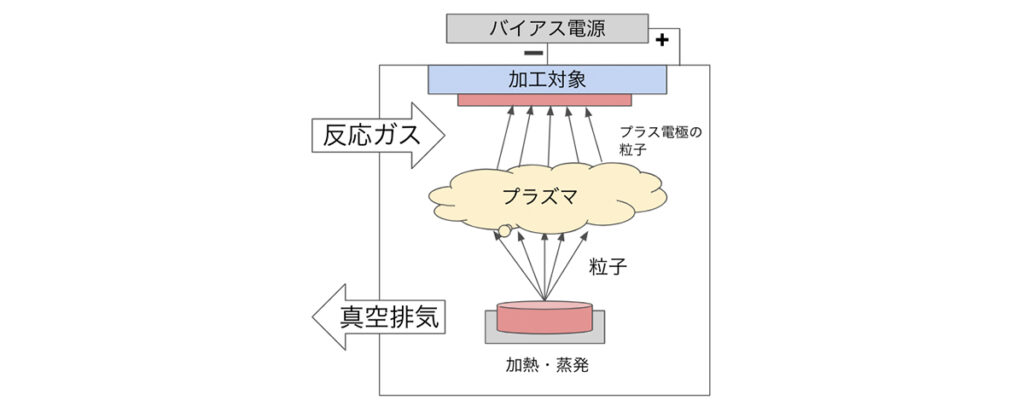
メリット | デメリット |
|
|
イオンプレーティングのメリットは、真空蒸着やスパッタリングに比べ、密着性の高い成膜ができる点です。しかし、設備コストが高いため、初期投資が大きくなることがあります。
PVDのメリット・デメリット|CVDとの違い
PVDとCVDは、薄膜を形成するための代表的な方法ですが、それぞれに独自の特徴と利点があります。
PVD | CVD | |
皮膜の原料 | 固体(プレート) | 気体(ガス) |
皮膜の種類 | 多い | 少ない |
成膜速度 | 遅い | 速い |
成膜温度 | 低い | 高い |
密着性 | 高い | PVDより高い |
化学物質のリスク | CVDと比べてほとんどない | 有毒性の高いガスを利用する場合がある |
皮膜の原料は固体
PVDの皮膜の原料は固体(プレート)なので、高純度の皮膜を形成することができます。一方、CVDは気体(ガス)を使用します。
皮膜の種類が多様
PVDは多元系の合金を含めさまざまな材料を使って、皮膜を形成することが可能です。これに対し、CVDは材料の種類が限られています。選択肢が豊富なことがPVDのメリットです。
成膜速度が遅い
CVDは、PVDの約10倍のスピードで成膜できると言われています。成膜速度の違いから、CVDの膜はPVDの膜より厚く生成されます。PVDで成膜スピードを速めるためには、「マグネトロンスパッタリング法」などの方法を選ぶといいでしょう。
成膜温度が低い
PVDは低温(200〜500度)での成膜が可能で、熱に弱い基板材料にも対応できます。CVDは高温(800〜1,000度)での成膜が必要であり、基板材料の選択に制約があります。高温処理ができると密着性は高まりますが、加工対象にダメージを与える恐れもあるでしょう。
密着性が高い
PVDは、密着性の高い皮膜を形成することができ、耐久性に優れています。一方、CVDはさらに高い密着性を持つことがあります。
化学物質のリスクがない
PVDは化学物質のリスクがほとんどないため、安全性が高いです。CVDは可燃性や有毒性のあるガスを使用する場合があり、安全管理が求められます。
PVDは物理的なプロセスであるため、化学物質による汚染やリスクが少なく、安全な操作環境を提供できます。
まとめ
PVDコーティングは、さまざまな材料に対して高品質な薄膜を形成できる優れた技術です。その方法には、真空蒸着、スパッタリング、イオンプレーティングがあり、それぞれにメリットとデメリットがあります。CVDとの違いを理解し、適切なコーティング方法を選択することが重要です。