Contents 目次
CAEとは
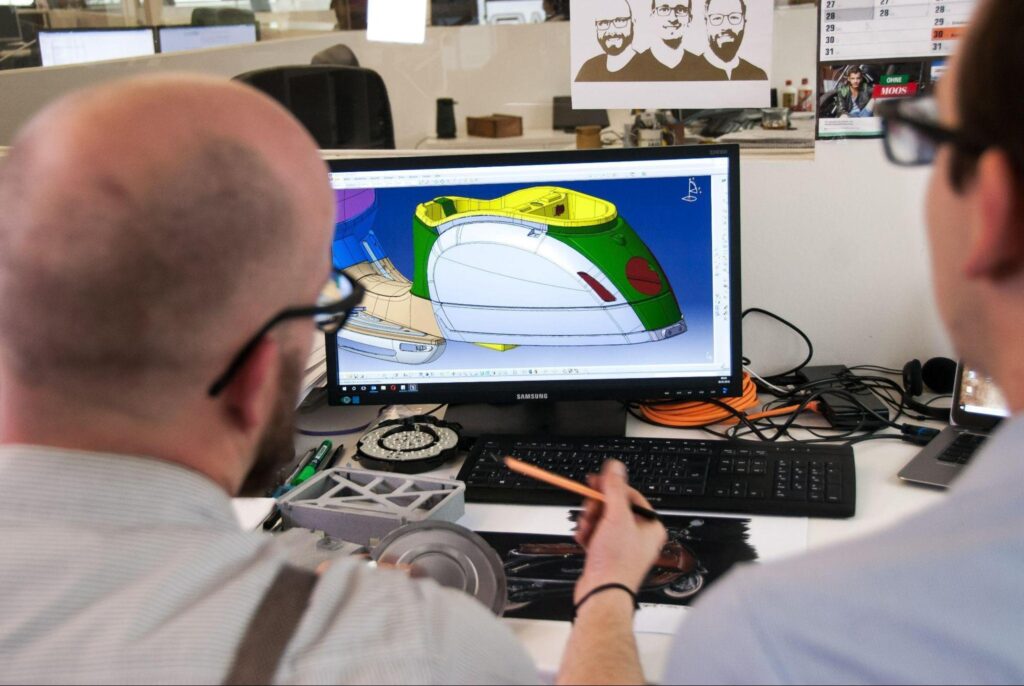
CAE(シーエーイー)とは、Computer Aided Engineeringの略語で、コンピューターを利用した工学支援システムを指します。
簡単に言うと、試験や実験を実際に行わなくても、コンピューター上でさまざまなシミュレーションを実施し、工学的な問題を解決できる技術です。
CAEの役割
CAEの役割は、実験や検証などを実際に行わなくても、コンピューター上でさまざまなシミュレーションを行うことでコスト削減や納期の短縮を図ることです。
例えば、自動車の開発現場における重要な評価基準の指標として「衝突安全性」があります。人に見立てた人形を座らせた自動車を、高速で壁に衝突させてどれほどの安全を確保できるか実験を行います。しかし、満足が得られる結果を得るためには何度も実験を行う必要があるため、大きな危険性を伴います。
CAEを活用すれば、バーチャルで実験をシミュレーションできるため、最適な部品の設計や発生リスクを検証できます。
このように、実際に検証や実験を何度もくり返さなくても、商品を開発する上での検証や予測を可能とすることがCAEの最大の価値です。エレクトロニクスや自動車などの開発だけでなく、医薬や食品などでも解析分野が広がっています。
CAEの役割は、物理的な実験が可能なケースで活用する一方で、実験が不可能な現象のシミュレーションンや、目に見えない物質の動きを可視化することでも活躍しています。
CAEが必要な理由
CAEが必要とされている理由は、製品販売後のトラブルの予防や不具合の原因究明が挙げられます。
製品の不具合に関するユーザーからのクレームはつきものですが、現代は情報化が進んでいるため、小さなトラブルでもSNSなどで企業のマイナスイメージがすぐに拡散されてしまう時代です。
そのため各メーカーは、些細な不具合でもすぐに改善する必要があり、トラブルが発生した場合は設計段階からの見直しが発生します。
設計からのやり直しが繰り返されるようになると、開発部隊には大きな負担がかかるため、新規のプロジェクト進行に大きく影響が出てしまいかねません。
CAEを活用すれば、あらゆるケースにおける検証を重ねられるため、未然にトラブルの発生率を下げられるようになります。
CAEの歴史
ここでは、CAEの歴史について年代ごとに解説します。
■~1995年
1980年前半頃にCAEソフトウェアの販売が開始され、トラブルシューティングとして活用されています。高度な専門知識と多くの手間が必要だったため、解析には専任者が必要でした。この頃のCAEの活用は、生産準備や試作のフェーズなど、設計プロセスの中でも下流の部分の利用にとどまることが一般的です。解析の際には、スーパーコンピューターや大型のコンピューターを必要としていました。
■~2000年
1990年代後半には、コストのカットや試作の回数を少なくすることを目的とし、仮想的な実験として活用されるようになっています。詳細フェーズでの利用へと広がりましたが、解析は専任者を必要とするため、属人的な課題は解消されていません。この時代では、UNIXを計算サーバーとして広く利用されるようになっています。
■2000年代~
2000年代に入ると、設計プロセスの早期の段階においても課題の抽出と対応策を可能とし、開発期間の短縮を目的とした利用が加速しました。使用する機器もWindowsサーバーが活用できるようになり、CAEのユーザーが設計を担えるようになりました。
CAEを活用した作業の効率化が注目され、ルーティン作業においては自動化をする技術が構築されています。
CAEを使用するメリット
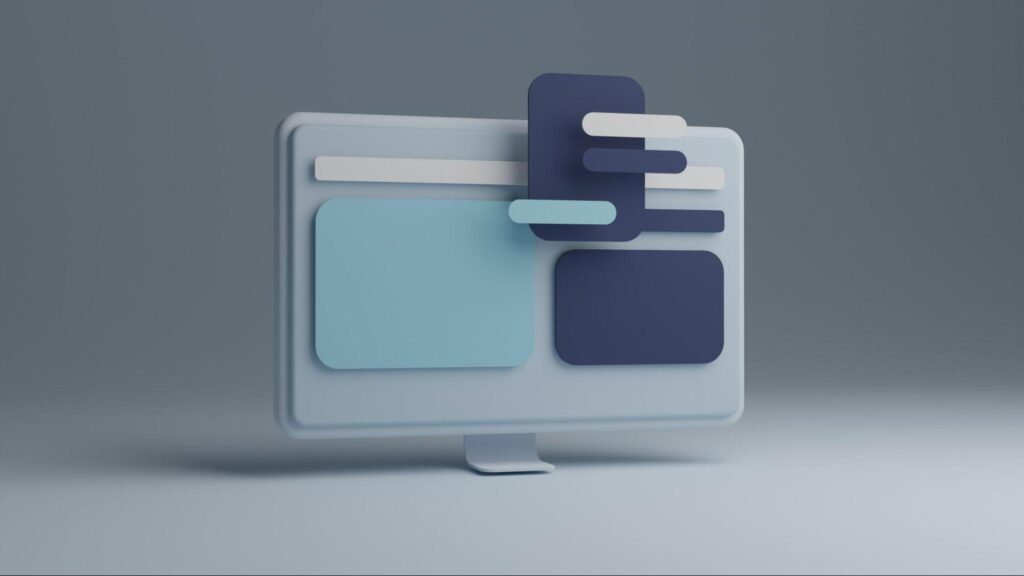
CAEを使用するメリットは、以下のようなことが挙げられます。
- コストの削減
- 難しい条件のシミュレーションの実現
- DXの推進
- 環境負荷の低減
- 開発期間の短縮
それぞれ詳しく解説します。
コストの削減
CAEを活用すれば、製品の開発にかかるコストを大幅に削減できます。CAEを活用しない場合、製品を製造するまでに、試作と実験を何度も繰り返す必要があります。
例えば、自動車の開発においては、1台の試作費用は10億円以上かかると言われています。多くの費用をかけて試作品を完成させても、その後さらに不具合が発生すれば再度設計の変更が必要となり、さらなるコストや工数がかかってしまいます。
CAEを導入すれば、試作品を製作しなくても設計の前段階で何通りもの機能や形状を測定し、耐衝撃性をシミュレーションできるため、早期の段階で不具合を特定できます。
それにより、開発期間や試作品を作成する物理的なコストや人件費を大幅に削減できます。
難しい条件のシミュレーションの実現
難しい条件でシミュレーションを行えることも、CAEの大きなメリットです。
例えば、宇宙レベルや原子レベルの実験や核分裂の実験など、再現が困難な環境での実験は、CAEを活用しなければ検証が難しいケースがあります。
CAEを活用して現実的には不可能なシミュレーションを実施することで、それまでの検証で気づけなかったことを発見し、新しいアイデアや技術が生まれることにつながります。
DXの推進
DX(読み方:デジタルトランスフォーメーション)とは、Digital Transformationの略語で、企業がデジタル技術を導入し、新しいビジネスモデルを通して顧客体験の変革を図ることで、新たな価値を創造していくことを意味します。
新型コロナウイルス感染拡大をきっかけに、DXは更に世間に浸透していきました。非対面での業務が必要とされる中、テレワークや在宅ワーク、リモートによる会議用ITツールの導入を迫られることで、企業におけるDXの推進が急務となったためです。
企業がDXを進める上で、特にデジタル化が求められているのは生産管理や製造部門、在庫管理や開発・設計分野です。DXの一環としてCAEを活用することで、業務の大幅な効率化を期待できるからです。
それにより、競合他社と差別化を図ることや、新たな価値やアイデアを作り出すことが可能となります。
環境負荷の低減
CAEの導入により、環境負荷を低減させることができます。それには、以下にあげる2つの理由があります。
- 大量廃棄を防げるから
- 環境を考慮した製品を製造しやすいから
■大量廃棄を防げるから
製品の種類や分野によって、開発段階における試験や実験の際に、廃棄物が大量に発生するケースがあります。例えば、自動車の衝突実験では、大破した自動車のボディやエンジン、部品などの廃棄物が生じます。
CAEを活用すれば、自動車を実際に大破させることは必要ないため、環境に配慮をしながら実験や実証を行えます。
■環境を考慮した製品を製造しやすいから
CAEを利用することで、環境問題に配慮した製品づくりが可能となります。例えば、照明機器を開発する際、部屋に必要な明るさを最低限のLDEの数によって設計できます。
自動車の開発においては、エンジンの適切なECU(電子制御装置)を設計することで、自動車の燃費向上が可能となります。
国連のSDGs採択により、環境問題への取り組みを強化すべき現代では、いち早くCAEを導入して環境に配慮した製品開発を推進する企業が増えています。
開発期間の短縮
CAEを導入することで、製品の開発にかかる期間や日数を短縮できることも大きな強みです。従来は、試作品を製作し、検証と実験を実際におこなうことで不具合を特定し、それを解消するために再び設計を繰り返すというプロセスでした。製品の精度を高めるためには、どうしても必要なプロセスでしたが、それでは多くの開発期間を要してしまいます。
CAEを活用することで、試作品を製作しなくともさまざまなシミュレーションが可能であるため、開発期間を大幅に短縮できます。それにより、競合他社よりも先んじて市場へ商品提供ができ、差別化を図りつついち早く収益化できるようになります。
CAEの活用分野
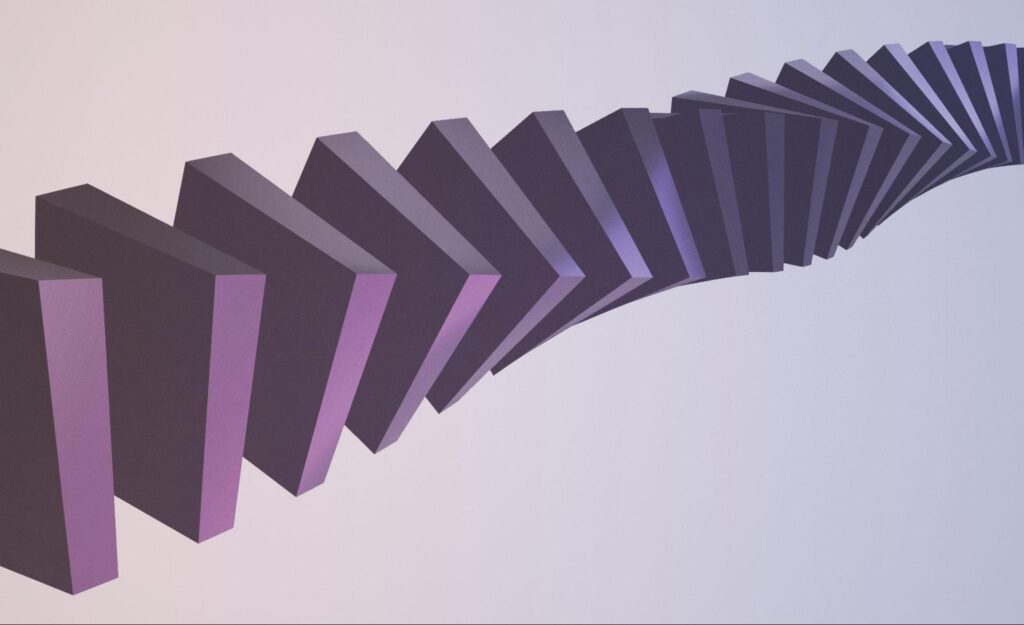
CAEの活用分野としては、代表的な以下の4分野があります。
- 構造解析
- 光学解析
- 電磁界解析
- 流体解析
それぞれ解説します。
■構造解析
構造解析とは、構造部材に生じる変形や応力などの力学性状を分析することを指します。簡単に言うと、構造物に負荷をかけた際に変形した具合を可視化し、それを分析することで適した部材や形状を検討する材料にします。複雑な構造計算をしなくても、CAEを使えば複雑な現象や形状の解析が可能となります。
■光学解析
光学解析とは、光の反射・屈折・分散を代表とした「光の動向」が、対象物体へどのように影響を与えるか分析することを意味します。CAEを活用することにより、光の色や明るさ、照射範囲などを可視化し、センサーやレンズの設計、空間設計に活用できます。
■電磁界解析
電磁界解析とは、対象物と電磁場の相互作用を解析することです。普段、生活において欠かせない電子レンジや冷蔵庫などの電化製品やスマートフォンは、電磁波が発生しています。他の製品との干渉や人体への影響を分析するため、開発段階においてCAEを活用した安全性の評価が必要になります。
■流体解析
流体解析とは、気体や液体がどのように流れるか、量や速度を表して解析することです。 空気の流れによって熱がどのように移動するか、流体力学を応用した分析です。
CAE活用の手順
CAEの活用においては、以下の手順で進めましょう。
- どのような製品を作るか決める
- 試作品を作って実験する
- 精算・販売を行う
- 保守点検・品質保証に活用する
それぞれ解説します。
1.どのような製品を作るか決める
まずどのような製品を作成するか、コンセプトを決めます。流行や生活スタイルを考慮し、市場が求めている製品を企画しましょう。最近では、企業がDXを推進している点や、環境への配慮をしていることから、物体がない状態で機能や性能を事前に評価できるモデルベース開発での設計への流れとなっています。
2.試作品を作って実験する
シミュレーションを重ねて製品の仕様が決まった後、試作品を制作して実験を行います。自動車の開発では、部品の形状が少しでも変化することで、耐久性や耐熱性に変化が生じます。CAEを使用して、性能とコストを配慮し、部品の形状や車全体のデザインを決定していきます。
実験の実施後、シミュレーションとの結果に違いが生じるようであれば、原因を特定して次回の実験、あるいは製品の制作時に変更・修正を行います。
3.生産・販売を行う
良い実験結果が得られた後、製品を生産し販売を行います。
例えば、自動車を販売する際、衝突時におけるエアバッグの安全性シミュレーションの解析結果がある場合、どのくらいの負荷に耐えられるのか、販売の際に根拠を説明できるようになります。
4.保守点検・品質保証に活用する
製品を販売する際は、CAEを活用していることが品質保証の裏付けとなるケースもあります。また、販売した製品にトラブルが生じた際、原因究明にCAEを利用します。
例えば、自動車を販売したケースで同じ部品ばかりが故障する場合は、部品の強度や耐久性をくり返しシミュレーションして問題を特定します。
CAEの課題と将来性
良いことばかりに思えるCAEですが、設計の3次元化が遅れているという課題があります。その背景には、CAEを活用できる技術者が補足していることが挙げられます。
CAEの導入時は、ソフトを利用してシミュレーションを繰り返し、結果を分析・解析して改善提案ができる人材の育成が必要です。体制が整うことで複雑な設計や仕様にも対応でき、開発スピードがアップすることで市場の変化に強い設計・開発体制をもつ企業として成長し、業界全体の競争力アップへとつながります。
まとめ
CAEを活用することで、実際に試作品を製作しなくても、コンピューター上でシミュレーションをすることで問題を特定でき、効率よく製品の開発を行えるようになります。市場へ製品を提供した後も、製品の同じ箇所で不具合が発生するようであれば、シミュレーションにより問題を特定し、改善することが可能です。
特に製造業界では、CAEを導入することで製造期間の短縮やコストの削減など、大きなメリットを享受できます。
技術者不足という課題をクリアし、積極的にCAEの導入を計画してみてはいかがでしょうか。