Contents 目次
プロフィール

日本板硝子株式会社クリエイティブ・テクノロジー部門ファンクショナルプロダクツ事業部フレークメタシャイン統括部
左:営業グループ グローバルセールスマネージャー 大場 裕史氏
右:技術グループ主席技師 日置 雅博氏
化粧品や自動車の塗装材に使われる高機能ガラスとは
NSGは、建築用ガラス、自動車用ガラス、高機能ガラス(クリエイティブ・テクノロジー)の3つの主要事業をグローバルで展開、世界各地の製造拠点や100カ国以上の販売網を有する世界最大級のガラスメーカーだ。
クリエイティブ・テクノロジー事業部門においては、独自技術を用い、地域や市場ニーズに即したガラス商材を展開し、ディスプレイや光学部品など、先端技術分野で使用される高付加価値な特殊ガラス製品の開発・製造・販売を行っている。その中でも、タイミングベルト用ガラス繊維やフレーク状ガラス、光輝性顔料などの開発を担うファンクショナルプロダクツ事業部が、リサイクル光輝材「METASHINE ECO®」の開発に成功した。まずはMETASHINE ECO®の従来品METASHINE®について話を聞く。
「ファンクショナルプロダクツ事業部では『ガラス組成』『成形・加工』『表面処理』といった基盤技術を組み合わせ、機能性材料などを開発しています。私たちが所属するフレークメタシャイン統括部ではフレーク状ガラス「ガラスフレーク®」と光輝性無機顔料「METASHINE®」を主な製品として取り扱っています。
ガラスフレーク®は耐食塗装、プラスチックの強化材が主な用途となっており、橋梁や風力発電など防錆のバリア材やプラスチック補強材としてあらゆる場所で活用されています。近年はプラスチック製品が軽量化されおり、それに対応して、当社のガラスフレーク®もより薄いものが求められています。
そのままでも工業材料して使われるガラスフレーク®ですが、このようなフレーク状のガラスに表面加工し、キラキラさせたものが光輝材「METASHINE®」です。アイシャドーや口紅などの化粧品や自動車や家電製品などさまざま製品の加飾材として活用されています」(大場氏)
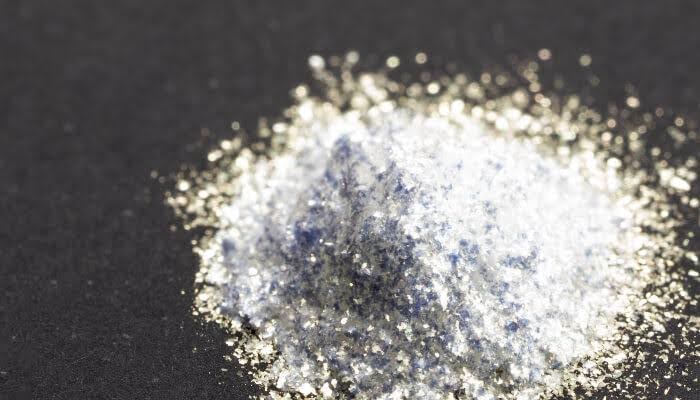
光輝材は、光を反射したり屈折させたりすることで、素材に輝きや光沢を与える材料の総称であり、その多くが塗料やプラスチックに混ぜて使用される。上述にあるように、化粧品のラメなど輝きや光沢の付与、自動車塗装や内装部品、家電製品、玩具、印刷インキなど用途は多岐にわたる。
なかでも、ガラスフレーク®を基材としたMETASHINE®は、ガラスの平滑性による強い輝度と高い透明感を両立し、雲母などに比べ、より強い輝きの表現を実現する。
「METASHINE®は2000年代、化粧品向けに上市されました。当時、光輝材の主流はマイカでしたが、ガラス基材のMETASHINE®はより力強い煌めきを得られると評判になりました。時代のニーズにも合致し、業界に広く浸透しました」(日置氏)
METASHINE®は、低アルカリ、低重金属、ボロンフリーである「TAガラス」を用いていることで、環境にも人にも優しい素材だ。NSG独自の成形技術により、フレークの厚みや形状などで光の振る舞いや肌なじみを自在に設計でき、ポイントメイクのように煌めきを持たせる用途だけではなく、くすみやシミなどをカバーするベースメイク向けパウダーにも用いられている。工業向けとしては、自動車のボディや内装、家電やモバイル端末の筐体、文房具など、多岐にわたる分野・製品で使用されている。METASHINE®は塗料や樹脂に添加することで、上品で鮮やかな色合いや、金属光沢など意匠性を高め製品デザインの表現を広げる。
自動車塗装では、光輝性顔料としてマイカやアルミナと並び、用途やデザインコンセプトに応じた選択肢の一つとして定着している。マイカが持つ柔らかで自然な光沢や、アルミナの高い輝度と彩度を活かした輝きが求められる場面もあれば、METASHINE®のように、透明感の中に鮮やかな光を宿す、奥行きのある輝きが適したシーンもある。特に、クリア感と輝きの両立が求められる場面や光の反射を精緻に設計したい用途では、METASHINE®がその強みを発揮する。ガラスフレーク®の粒度を緻密に制御することで白ボケ*を防ぎつつ、狙った質感を高い再現性で実現できる点が評価されている。
※塗装面に白濁や艶の喪失などが見られること。
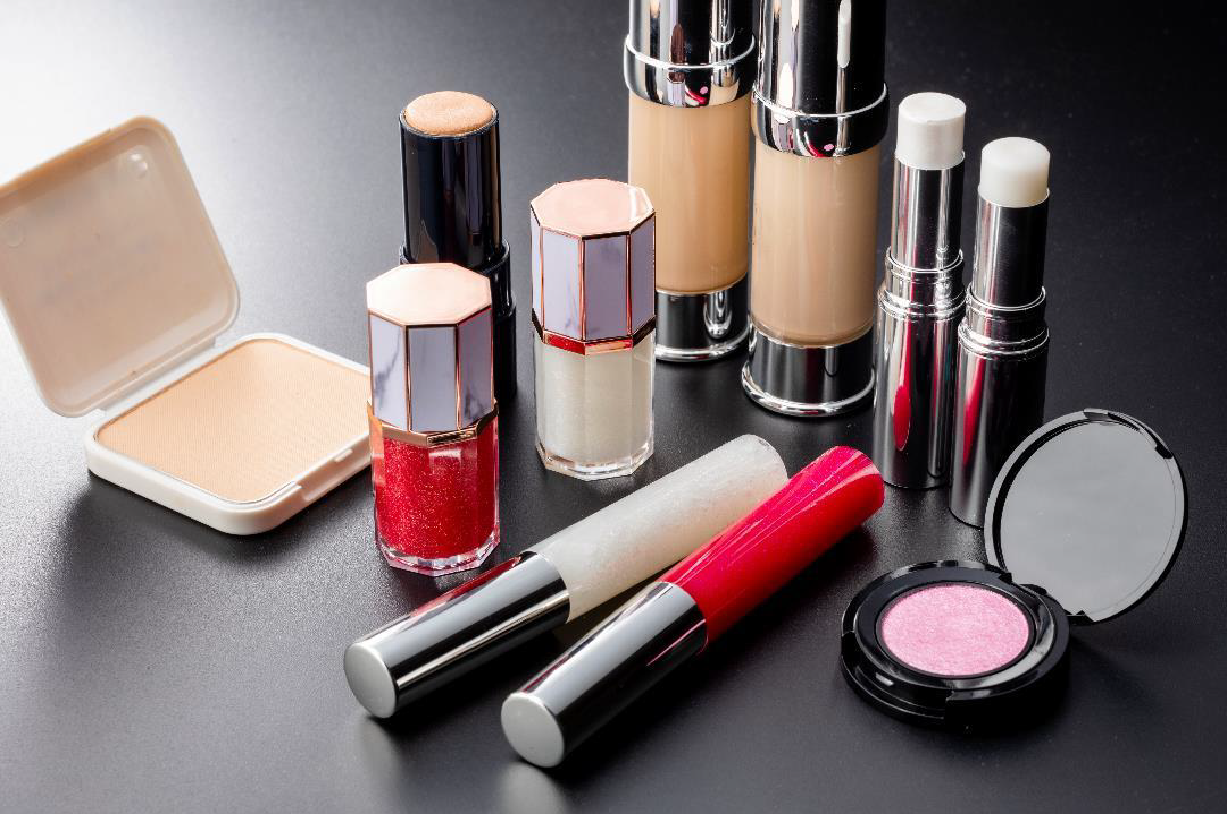
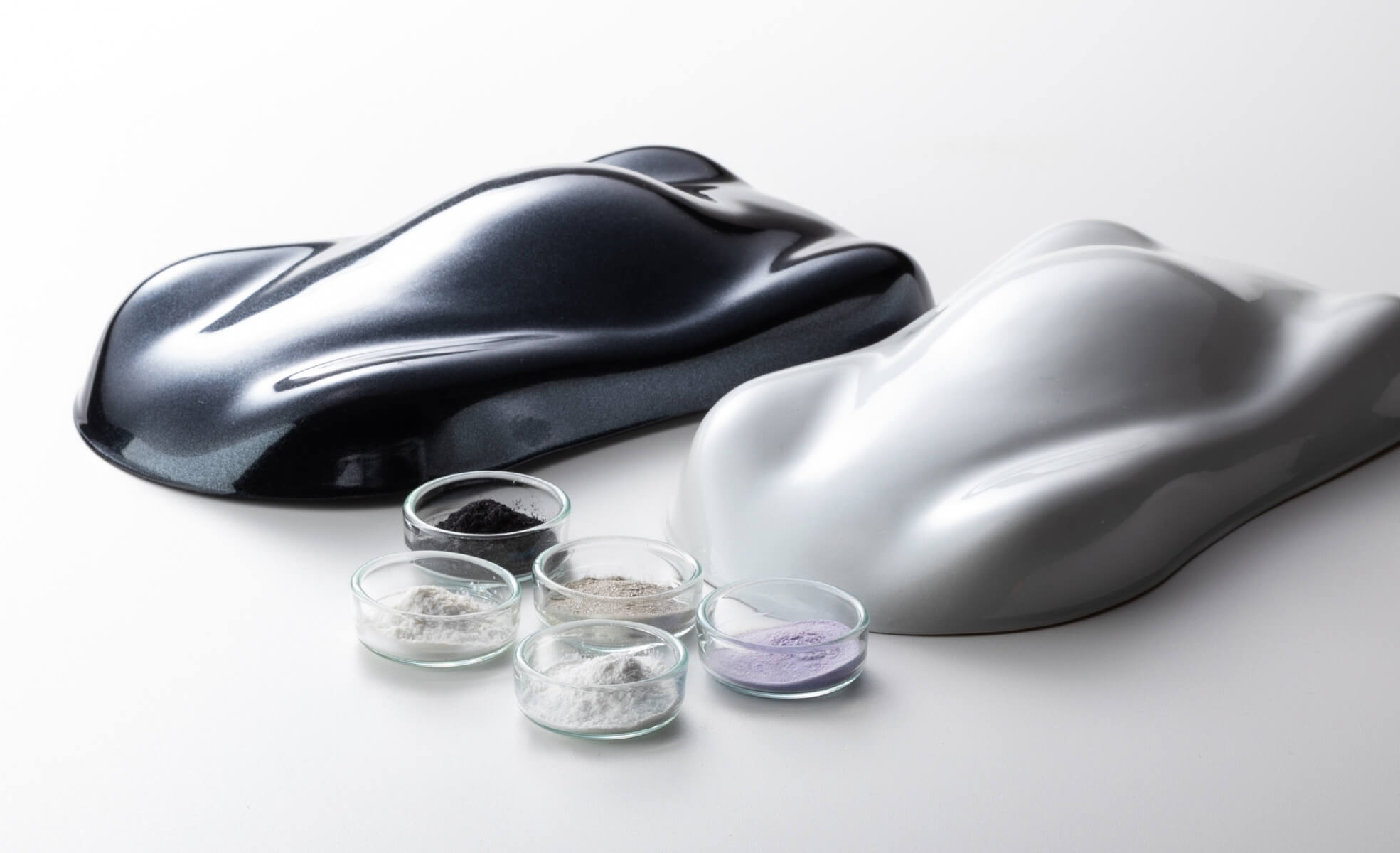
ガラスという素材だからこそ実現した「METASHINE ECO®」
自動車用途での順調な拡販が進む中で、国内外の自動車業界における脱炭素の動きが活発化していた。そのような状況の中、自動車業界向けに製品を提供する塗料メーカーから「環境負荷低減につながる材料を探している」との問い合わせが寄せられたことが、METASHINE ECO®開発のきっかけとなった。
この要望を受け、NSGではガラスメーカーとしての視点から、METASHINE®で使用するガラスフレーク®にリサイクルガラスを活用するというアイデアを提案。2023年同社舞鶴事業所におけるフロート板ガラス製造時のガラス端材を活用したガラスフレーク®製造の研究に着手。2024年12月、その開発の成功を発表した。従来品(METASHINE®)と比較して、製造時のCO₂排出量を最大3割削減することが可能する、リサイクル基材を使用した業界初の光輝材が誕生した。
「ガラスだったらリサイクルできるんじゃないかと、古来よりリサイクルできる材料として使われてきたガラスと言う素材に期待を寄せて頂いた。光輝材の中でリサイクルできる原料はアルミぐらいしかない。酸化チタンをコーティングしたパール系光輝材ではガラス以外、リサイクルが難しい。リサイクル基材を使用した業界初の光輝材ということで、塗料メーカーさんからはすぐにサンプル評価したいと引き合いを頂きました」(大場氏)
NSGは、新中期経営計画「2030 Vision: Shift the Phase」における戦略方針の1つとして「Decarbonization(脱炭素化)」を掲げている。持続可能な社会の実現に貢献するため、社内生産工程からサプライチェーン全体にまで及ぶ脱炭素化に取り組んでいる。このような脱炭素化における施策としても「METASHINE ECO®」のコンセプトに期待が寄せられた。
日置氏によれば、これまで、廃棄されていた端材を原料として使用するため廃棄ガラス削減に加え、リサイクルガラスは通常のガラス原料よりも低い温度で溶融可能であり、ガラスフレーク成形時のエネルギー消費を大幅に削減できる。また、ガラス原料には炭酸カルシウムや炭酸ナトリウムが含まれており、溶融時の加熱によってCO₂が多く発生するが、リサイクルガラスであればこれらの成分がすでに抜けているため、溶融時にCO₂が発生しないという利点があると言うことだ。
「従来、METASHINE®の原料は外部のメーカーから調達していました。METASHINE ECO®では社内で発生するガラス端材が原料として利用できるため、原料調達輸送時に発生するCO2も削減できます。採掘、海上輸送、混合、溶融までの製造プロセスで使用されるエネルギー量の削減によって、CO2発生量を従来品比で最大30%削減できると試算しています」(日置氏)
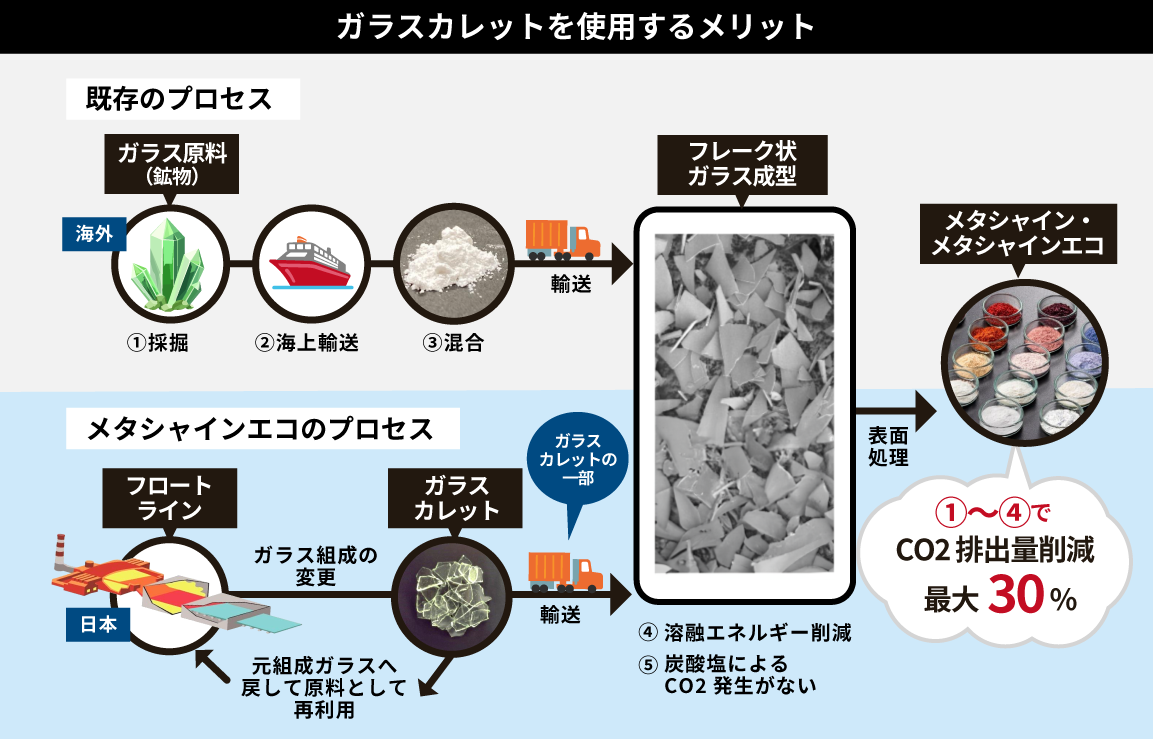
ダウンサイクルからアップサイクルへ
従来品比でCO2発生量が最大30%削減できるーーこの大きな削減効果のポイントはリサイクルガラスの調達にあると言う。
「開発において材料となるリサイクルガラスをどのように調達するかに一番苦労しました。高機能ガラスとして使用できる品質、一時的な活用ではなく量産化に対応できる安定調達の検討も必要でした」と日置氏。
NSGの板ガラスは「フロート製法」を採用しており、この製法では、溶融窯でガラス原料を溶かし、フロートバス内の溶けた錫(すず)の上に流し込んで平らに成形し、徐冷窯でゆっくりと冷却する。生産工程で発生する不用なガラスは粉々に砕いて「ガラスカレット」とし、直接窯に戻してリサイクルされてきた。日置氏はこのガラスカレットを、METASHINE®の基となるガラスフレークの原料としても活用できないかを考えた。
「NSGのフロート窯は、千葉事業所(千葉県市原市)と舞鶴事業所(京都府舞鶴市)にあります。ガラスカレットの有効活用の可能性を確認したところ、千葉事業所ではカレットの完全リサイクル化が出来ていて使い道には特に困っていませんでしたが、舞鶴事業所では組成切り替え時の中間組成の扱いが困りごとになっていたことが分かりました」(日置氏)
生産する品種を切り替える際、それぞれの品種で用いる組成の異なるガラスの入れ替えが行われるが、その時に排出されるガラスカレットは、組成が入れ替わる最初の方と最後の方のごく一部しかリサイクルに利用できない。異なった組成が混じりあう状態では、狙った板ガラスの特性が得られないためだ。
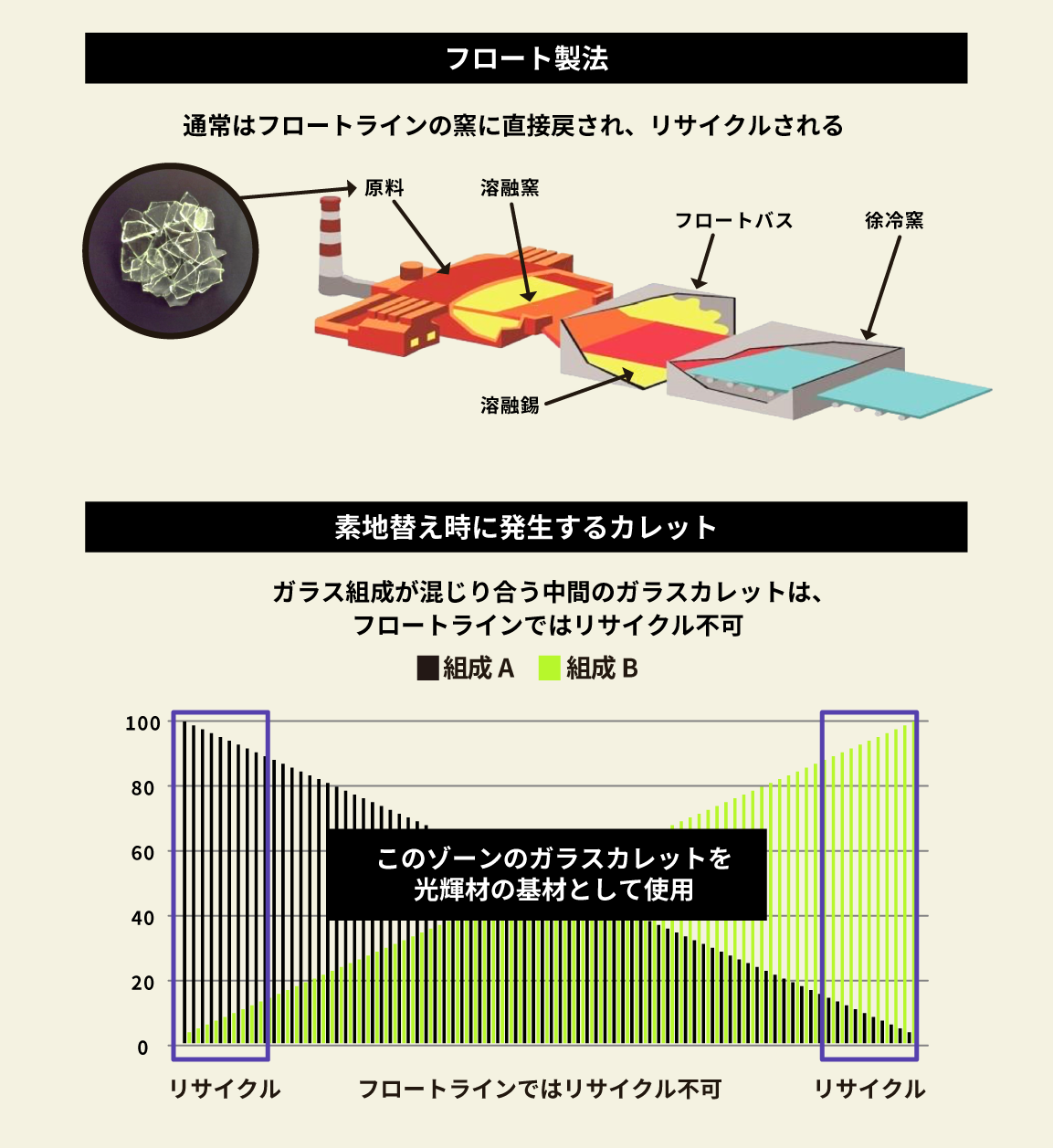
このような生産工程内でリサイクルできないガラスカレットは、工場の外で建築資材の一部、道路舗装の骨材、断熱材などに使用することでダウンサイクルされてきた。METASHINE®の原料とすることができれば単なるリサイクルではなく、アップサイクルという新たな価値を提供できる。こうして原料となるガラスカレットの安定調達が見込めたことで、2023年の後半からリサイクルガラスフレークの試作に着手。顧客にもそのサンプルを試してもらいつつ開発を進めた。
「舞鶴事業所のフロートラインから排出されるガラスカレットの組成のばらつき分析や、カレットの溶融条件、回収方法まで丹念に検証しました」と日置氏。最も懸念したのは、従来のガラスフレーク®の原料は微小な粒子だったため、ガラスカレットのような塊を用いるのが初めてであったことだ。
「粒子とカレットでは溶融条件が大きく異なり、かつカレット自身の大きさもさまざまであるため、従来のガラスフレーク®の生産設備で適切な取り扱いができるかどうかを心配しました。当社にはガラス技術、分析シミュレーションを基盤に製品とプロセスを創出する研究開発の中核拠点技術研究所(兵庫県伊丹市)があります。そこの研究員と相談しながら試験を行い、ガラスフレーク®生産を想定した際のさまざまな懸念点をつぶしていきました」
そして、約半年間かけてさまざまな形状やサイズのガラスカレットを用いて実験を地道に繰り返して、リサイクルガラスフレーク生産の技術を確立した。2024年の秋ごろにはリサイクルガラスフレークに酸化チタンコーティングを施す試作にも成功し、報道発表に至っている。
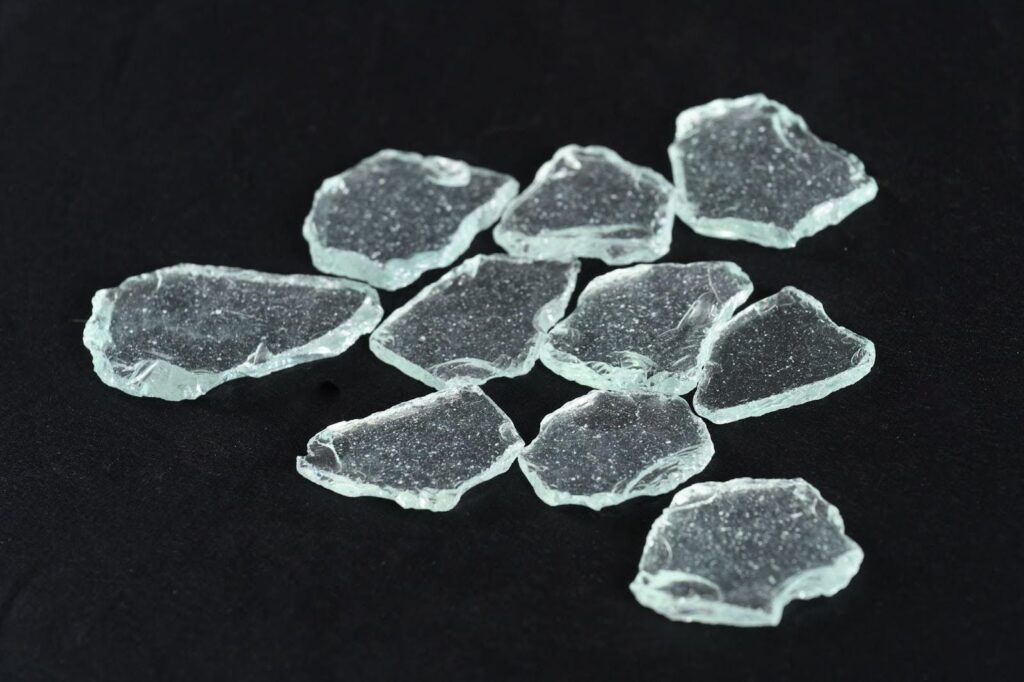
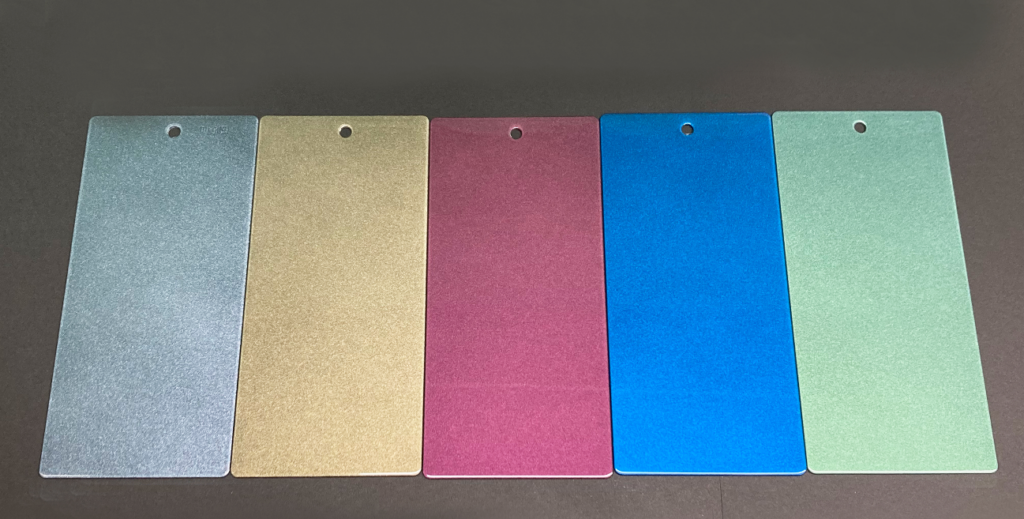
イノベーションの鍵は社内連携と目線のすり合わせ
METASHINE ECO®の開発は、高機能ガラスを開発・製造するファンクショナルプロダクツ事業部を発起人として、自動車用ガラスを取扱う舞鶴工場、技術研究所など部門間の壁を乗り越え、コラボレーションすることで、新たな価値を生み出した好事例と言えるだろう。しかし、はじめからスムーズな部門横断がスタートできたわけではなかったと言う。
「各部門は、扱う製品、技術、顧客が異なるため、仕事に対する考え方や感覚に大きな隔たりがありました。例えば、リサイクルに対する意識一つをとっても、建材や自動車部品向けに大量のガラスを扱う部門と、微細な製品を扱うファンクショナルプロダクツ事業部では、全く異なっていました。『屋外で保管しても問題ない』という部門と、『ミクロン単位での品質管理が必須』と互いの常識が壁になりました。プロジェクトを進めるうえで感覚のすり合わせの重要性を感じました」(日置氏)
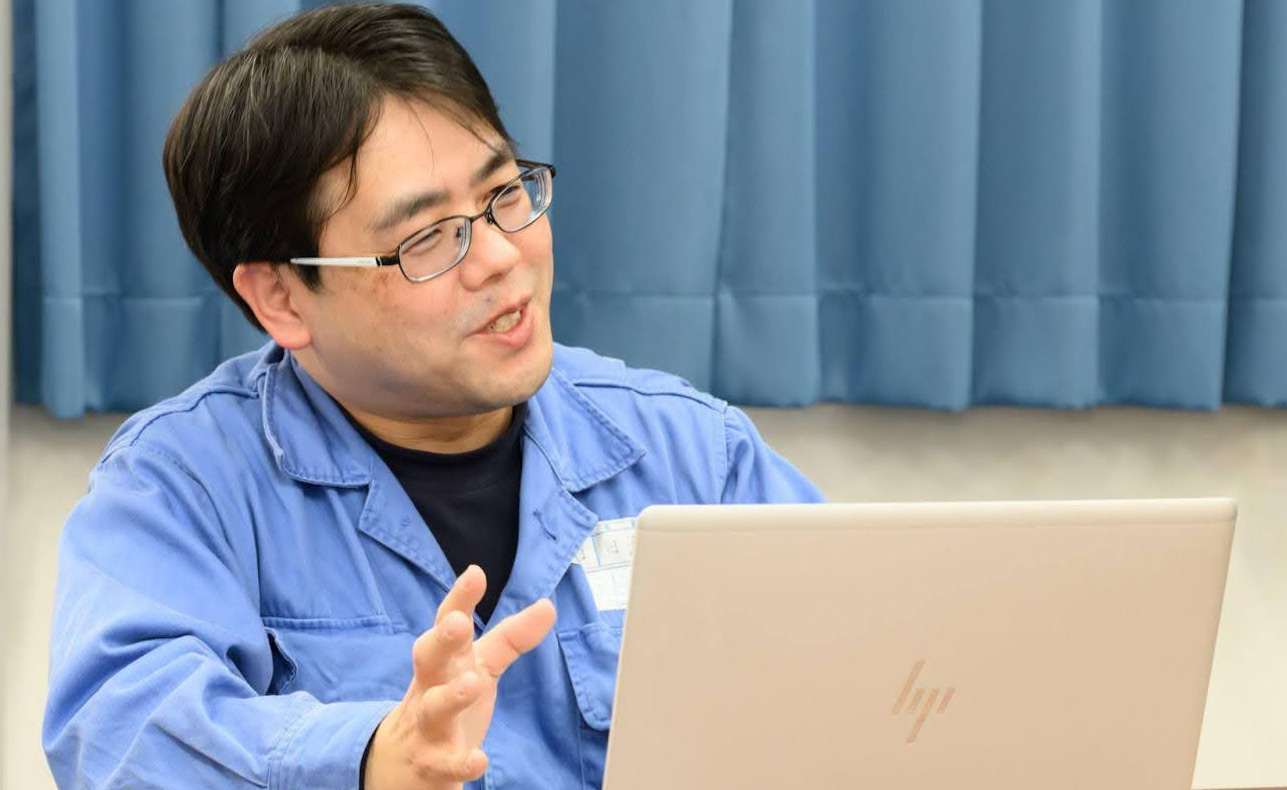
大場氏は自身の役割を、顧客のニーズを技術部門へ伝え、社内でプロジェクトの重要性を訴えることだと話す。実際の開発や現場との交渉を担当した日置氏に対し、大場氏はプロジェクトの必要性や提供価値を社内で理解してもらうことに奔走した。
「当初、部門間の壁や各部門の目標の違いから、協力体制を築くのは簡単ではありませんでした。しかし、このプロジェクトを立ち上げるためには、各部門の連携が不可欠です。上長の協力を得て、各部門への働きかけを強化しました。
当時、NSG全体でCO₂排出量削減への意識が高まっていましたが、各事業部門は具体的なアイデアを模索している状況でした。そのような中で、ガラスのリサイクルだけでなく、アップサイクルという新たな価値を提示できたことが、プロジェクト推進の鍵となりました。さらに、お客様の声が後押しとなり、共通のゴールを示すことで、多くの共感者と協力者を得ることができました。そして、何よりも日置さんの粘り強い交渉と各部門への丁寧な説明が、プロジェクトを前進させる原動力となりました」(大場氏)

サステナブルなストーリーに対応できる製品を送り出したい
現在、METASHINE ECO®は自動車用途に限定したサンプル評価を進めている段階にある。自動車分野では耐候性の評価に2年以上時間を要することもあり、その間に、NSGでは生産技術の確立を進め、2026年中の上市を目指す。具体的には、従来の生産設備の改造や工程自動化に取り組むことで、将来的な拡大展開に備えていく。
METASHINE ECO®のサンプル品を試した顧客の期待は大きいものだったと言う。「光輝材でマイカやアルミナを基材としたものは、原料となる鉱物の採掘や輸送をしなければなりません。さらに2000℃以上を超える再溶融の工程が必要で、CO2を大量に排出してしまいます。そのため現実的にリサイクルには適さないとされてきました。これまでリサイクルによる光輝材が市場に存在しなかったため、お客さまからの評判は上々でした」(大場氏)
上市後しばらくは、主に自動車向け生産設備からガラス端材を調達することから自動車塗料向けをターゲットに工業用途として販売する。市場創出のため、従来製品と同等の価格設定を目指す。将来的には自動車以外のさまざまな産業向けや、塗装以外の成形品向けへの展開も視野に入れ同様のリサイクルコンセプトを適用できるかを検討していく。
「現状は、工業用ガラスカレットをベースとしており、重金属の含有量が多いことから、化粧品用途には適していません。クリーンなガラスがあれば、化粧品への展開も可能ではありますが、こちらもどこから原料を調達してくるかが課題にはなります。技術的に実現可能な範囲を見極めながら、対内的にも対外的にも展開の可能性を探っていきたい」(日置氏)
今回開発したものは酸化チタンの被膜を用いたものだが、「METASHINE®」シリーズには酸化鉄や銀の被膜を施した製品もあり、今後はそうしたバリエーションにも対応を模索する。さらに、ファンクショナルプロダクツ事業部では、CO₂削減にとどまらず、サステナブルなストーリーに対応できる製品のラインアップ拡充を進めていく。
「まず樹脂補強用のガラスフレーク製品群では、樹脂製品の小型化・軽量化のニーズを受けたガラスフレーク®の薄型化です。最も薄いもので0.35ミクロンという厚みまで生産可能で、軽量化によって求められる強度や寸法精度への対応を提案しています。
また、塗装レス化の影響等で滑らかな表面性ニーズも増加しており、意匠面のざらつきを防ぐためガラスフレーク®の粒径もさらに細かにできないか検討しています。METASHINE®では、ガラス厚みを逆に厚くすることで樹脂成形時のウェルドラインやフローマークなど成形不良を目立たなくするような用途などで提案できると思っています。
化粧品のベースメイク向けに開発された製品群「MAR’VINA®(マルビナ)」では、フレーク状、粒状のガラス成形技術を背景に、マイクロプラスチック規制が強まる市場にプラスチック代替素材として拡販を目指します」(大場氏)
NSGファンクショナルプロダクツ事業部はリサイクル技術を進化させ新たな製品開発により環境負荷低減と経済性両立への挑戦を続ける。これらの取り組みのその先に、リサイクル由来の素材が、私たちの身近な製品として当たり前に使われている未来が待っているのかもしれない。